자동차 공장의 공정혁신을 이루기 위해 윤자영 한국자동차연구원(이하 한자연) 정책전략실 책임연구원은 자동차 기업과 설비 기업 간 긴밀한 협업을 통해 국내 노동여건, 작업환경 및 작업자에 최적화된 설비를 우선적으로 공급받을 수 있도록 산업 간 공동연구개발 및 유기적인 네트워킹이 필요하다고 분석했다.
스마트제조화 통해 배터리 제조 정밀성 ↑·빅데이터 분석 활용 생산 최적화 진행
수요 변동성 증가 따른 리드타임 단축 필요성 ↑…장비고도화·데이터 관리 투자 이끌어
세계 자동차 기업들은 제품경쟁력 제고와 비용 절감을 위하여 장비 고도화, 공정 및 물류 자동화 도입 등 적극적으로 공정개선 중이며, 특히 중국은 자동차산업의 질적 고도화를 위하여 스마트 제조화에 주력하고 있으나 우리나라는 아직 공정혁신을 이룬 기업이 없다고 세계경제포럼(WEF)은 판단했다.
자동차 공장의 공정혁신을 이루기 위해 윤자영 한국자동차연구원(이하 한자연) 정책전략실 책임연구원은 자동차 기업과 설비 기업 간 긴밀한 협업을 통해 국내 노동여건, 작업환경 및 작업자에 최적화된 설비를 우선적으로 공급받을 수 있도록 산업 간 공동연구개발 및 유기적인 네트워킹이 필요하다고 분석했다.
윤자영 책임연구원은 ‘등대공장을 통해 본 자동차 제조공정 혁신 동향’을 주제로 한 산업분석 Vol.135에서 자동차 선진국들은 가치사슬 전반의 디지털 전환으로 첨단 제조설비 구축에 주력하고 있으며, 전동화, 자율화로의 자동차 전환 시장 선점을 위해서는 생산현장에서의 변화가 중요한 경쟁요인이라고 강조했다.
세계경제포럼은 글로벌 컨설팅 기업 맥킨지와 2018년부터 기술개발척도, 인적구성 등 평가를 통해 매년 두 차례 고도화된 제조 현장으로서 등대공장(Light House Factories)을 선정했으며 2023년 12월 기준 전세계 등대공장은 153개다.
※등대공장 : 등대가 배를 안내하는 것처럼 IoT, 클라우드 컴퓨팅, 빅데이터, AI 등 4차 산업혁명의 핵심기술을 활용해 제조업의 혁신을 이끄는 공장을 의미
윤자영 책임연구원은 2019~2023년 기간 동안 세계경제포럼에서 발표한 등대공장 중 자동차기업이 추진한 주요 내용과 성과를 토대로 공정혁신의 유형과 성과를 파악한 결과를 공유했다.
전체 등대공장 중 배터리 기업을 포함한 자동차산업 내 기업은 총 17개로 전체의 11.1% 비중을 차지하여 전기전자, 바이오 및 의료기기산업에 이어 세 번째로 많은 산업군으로 나타났다.
자동차 부문에서는 자율제조 및 전동화 수요 충족은 물론, 부품 공용화(모듈 아키텍처)를 통한 원가 혁신, 개별 수요자가 원하는 맞춤형 제품 등 다양화에 대응하기 위해 첨단기술을 활용함으로써 다양한 생산방식 도입이 활발하다.
전동화 수요 충족을 살펴보면 스마트제조화를 통해 전동화의 핵심인 배터리 제조의 복잡성, 정밀성을 높이고, AI, 머신러닝 기술을 활용하여 부품의 모듈화 구현, 빅데이터 분석을 활용한 품질관리, 생산 최적화를 진행하는 추세를 보였다.
자동차 등대공장을 국가별로 살펴보면 중국이 10개로 가장 많은 비중(58.8%)을 차지하고, 프랑스 및 튀르키예 2개, 인도, 브라질, 독일에사 각 1개씩 선정되었다.
우리나라의 경우 포스코, LG전자, LS일렉트릭 등이 등대공장으로 선정되었으나 자동차 분야는 아직까지 없다.
중국은 2015년부터 ’중국제조 2025‘를 바탕으로 국가 차원에서 전 제조업에서의 스마트제조를 확산시키기 위해 구체적인 계획과 목표를 설정 및 추진하였고, 각 지방정부에서 구체화된 행동지침을 실행한 바 있다.
스마트제조 역량 성숙도를 모델을 구축하여 일정 규모 이상의 제조공장은 70% 이상 디지털화 및 네트워크화를 실현하도록 하고 스마트제조 시범공장을 500개 이상 건설하여 등대공장 비중이 높은 것으로 파악되었다.
제조분야별로는 르노 3개 공장, BMW, SAIC 등 완성차 기업 6개와 Bosch 4개 공장, CATL 3개 공장, CITIC Dicastal, CEAT 등 부품사 11개 공장으로 분석되었다.
기업들은 △노동력 부족 △공급망 리스크 △비용압박 △탄소중립 등 산업변화에 대응하고, △불량률 감소 △제품 다양화 △제조 속도 개선 등 소비자 만족도를 높이기 위하여 장비 예지보전시스템, 디지털트윈, 머신러닝 기능 활용하고 있다.
대표적으로 중국의 CATL은 급증하는 이차전지 수요 및 인건비 해결, 제조과정에서의 탄소중립을 위하여 △빅데이터를 활용한 품질 시뮬레이션 △적층제조 방식으로 전환시간 감소 △AI 비전기술 활용으로 미크론‘(10-6m)’ 수준의 품질검사 △딥러닝(프로세스 제어 및 에너지 관리) 등을 활용했다.
결과적으로 생산량 320% 증가, 제조비용 33% 감소, 탄소 배출량 47.4% 감소, 품질결함 99% 감소 등 성과를 시현했다.
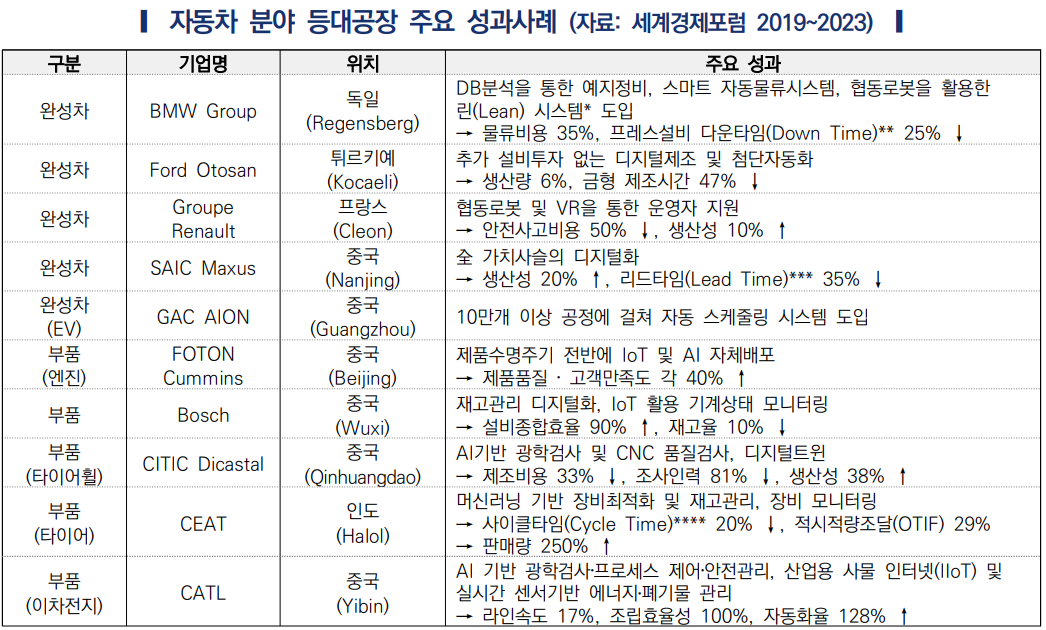
▲자동차 분야 등대공장 주요 성과사례(자료 출처: 한국자동차연구원 산업분석 Vol.135)
공장별로 추진한 공정혁신을 유형화하여 구분한 결과, 장비고도화 28.4%, 데이터 관리 25.7%, 공정․물류자동화 17.6%의 순서로 나타났다.
자동차산업은 다양한 소재, 부품 및 공정이 필요한 조립산업으로 공정 간 협력 효율이 중요한 경쟁력이고, 소비자 수요의 변동성 및 다양성이 커짐에 따라 시장 출하까지의 리드타임을 단축시킬 필요성이 증가하여 기업들이 장비고도화 및 데이터 관리에 투자를 지속하고 있다.
또한 부품조달, 운반의 자동화와 AMR(Autonomous Mobile Robots) 등 무인이동체 활용을 확대시켜 물류 혁신을 추진하고, 이를 통해 적시 부품조달 및 재고 최적화 효과도 톡톡히 보고 있다.
한편 수요와 생산데이터를 연계하거나 가상과 현실이 융합된 데이터 연계 및 디지털 트윈 분야는 상대적으로 본격 도입사례가 적은 편인 것으로 나타났다.
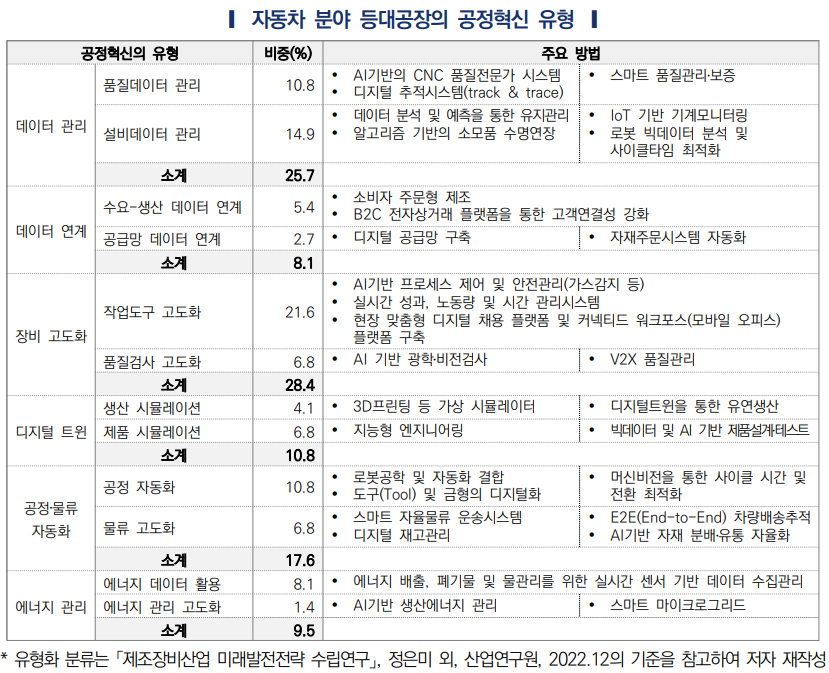
▲자동차 분야 등대공장의 공정혁신 유형(자료 출처: 한국자동차연구원 산업분석 Vol.135)
윤자영 책임연구원은 “가치사슬 전반의 디지털 전환으로 자동차 선진국들은 첨단 제조설비 구축에 주력하고 있으며, 전동화, 자율화로의 자동차 전환 시장 선점을 위해서는 생산현장에서의 변화가 중요한 경쟁요인”이라며 “제조과정에서의 방대한 데이터를 활용하여 효율성을 높여 시장에서의 가격 경쟁력을 확보하고, 제조설비의 다운타임 및 재설계 업그레이드를 포함한 소재, 부품 전환을 신속하게 수행해야 한다”고 분석했다.
이어 “이를 위해서는 자동차 기업, 설비 기업 간 긴밀한 협업을 통해 국내 노동여건, 작업환경 및 작업자에 최적화된 설비를 우선적으로 공급받을 수 있도록 산업 간 공동연구개발 및 유기적인 네트워킹이 필요하다”고 전했다.