한국재료연구원 금속재료연구본부 타이타늄연구실 이상원 박사 연구팀이 한스코·부산대·에스앤더블류·진영TBX 등 산·학·연 공동연구를 통해, 차세대 복합가스터빈 핵심부품인 타이타늄 압축기 블레이드 제조기술을 국산화하는 데 성공했다.
대형 타이타늄 압축기 블레이드 제조기술 개발
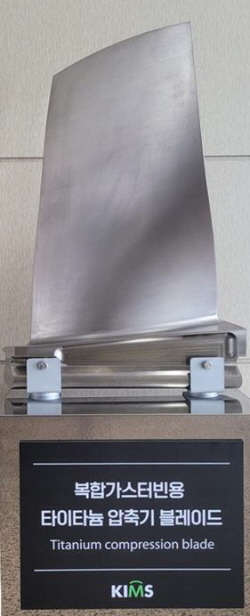
과학기술정보통신부 산하 정부출연연구기관인 한국재료연구원(KIMS, 원장 이정환)이 전략 수입에 의존하던 발전터빈용 타이타늄(Ti, 티타늄) 핵심부품을 국산화하며, 국내 타이타늄 기술 자립화가 기대된다.
재료연은 금속재료연구본부 타이타늄연구실 이상원 박사 연구팀이 한스코·부산대·에스앤더블류·진영TBX 등 산·학·연 공동연구를 통해, 차세대 복합가스터빈 핵심부품인 타이타늄 압축기 블레이드 제조기술을 국산화하는 데 성공했다고 4일 밝혔다.
타이타늄 압축기 블레이드는 넓은 유로(flow path)에서 대기 흡입과 압축을 할 수 있고, 기존 철강 소재와 비교해 공력성능 측면에서 효율적으로 고온/고압의 공기를 연소기에 공급 가능해, 차세대 복합가스터빈의 에너지 고효율을 달성하기 위한 핵심부품이다.
기존 압축기 블레이드를 철강에서 타이타늄으로 대체할 경우, 에너지효율이 약 0.1% 상승할 것으로 예상된다.
이는 가스터빈 1기당 연간 수백만 달러의 경제적 가치를 갖는 수치이다. 이러한 이유로 최근 개발된 세계 최고 에너지효율을 가진 해외 가스터빈 모델에는 타이타늄 압축기 블레이드가 적용되고 있다.
이 기술은 고강도 타이타늄 합금(Ti-6Al-4V)으로 28인치급 대형 압축기 블레이드를 제조하는 기술이다. 소재부터 부품 제조에 이르기까지 전주기 공정(용해→중간재→형단조→가공)을 순수기술로 제조해 기술 자립화를 이루고 제조 가치사슬을 국내에 구축했다는 점에 의미가 있다.
연구팀은 소재에서 부품에 이르는 공정 전반에 걸쳐 국내 보유 인프라만으로 제조할 수 있도록 진공용해 해석, 가공열처리 공정설계를 수행했고, 각 공정 제품의 기계적/화학적 평가를 통해 국산 타이타늄 블레이드의 신뢰성 확보를 지원했다.
특히 각 제조공정의 가치사슬이 국내에서 연결되도록 해, 가격·납기·품질 개선으로 국산 제품의 경쟁력을 높였다.
최근 들어, 이산화탄소(CO2) 배출규제와 국내 에너지 수입 의존도 감소 등 복합가스터빈의 에너지효율 향상을 위한 요구가 높아지고 있다.
가스터빈의 연소온도와 압력 증가는 물론, 이를 위한 터빈 블레이드의 대형화가 꼭 필요하다.
기존 내열 철강 소재는 부품 대형화에 따른 무게 증가로 회전 중 부품 파단 가능성이 커 고강도 경량 금속 소재인 타이타늄 합금으로 대체되고 있지만, 이마저도 국내 기술 및 관련 인프라 부족으로 해외에서 전량 수입되는 실정이다.
우리나라는 세계 다섯 번째로 가스터빈 독자 모델을 개발했으며, 현재 에너지효율 63%의 복합가스터빈을 개발하고 있다. 정부 또한 2030년 글로벌 가스터빈 4강을 목표로 추진전략을 공개한 바 있다. 개발한 제품은 국내 가스터빈 발전과 그 방향이 일치하며 세계 최고 수준의 국산 가스터빈 개발에 이바지할 수 있을 것으로 기대된다.
연구책임자인 재료연 이상원 선임연구원은 “타이타늄을 이용한 가스터빈 블레이드 대형화는 친환경 복합가스터빈 개발을 위해 꼭 필요한 기술”이라며 “본 기술은 그동안 개발이 어려웠던 국방·항공·우주용 대형 타이타늄 부품 국산화에도 빠르게 적용할 수 있어 그 파급효과가 클 것으로 기대된다”고 말했다.
본 연구성과는 산업통상자원부 소재부품기술개발사업(1,250MPa급 고비강도 타이타늄 합금 대형 블레이드 제조기술 개발)의 지원을 받아 수행됐다.
현재 수요기업인 ㈜두산에너빌리티는 해당 국산 타이타늄 블레이드를 다수 구입해 사업화를 위한 신뢰성 평가를 수행하고 있으며, 차세대 국산 가스터빈 모델 적용을 검토 중이다.
또한 연구팀은 이와 함께 제품의 가격, 품질, 납기 경쟁력 향상을 위한 공정개선 연구를 추가로 진행하는 등, 타이타늄 블레이드 양산화시기를 앞당기고자 노력하고 있다.