텍사스 인스트루먼트(TI)가 미국 텍사스주 댈러스에 위치한 기존 GaN 제조 시설에 이어 일본 아이주 팩토리를 본격 가동하며, GaN(갈륨나이트라이드) 전력 반도체의 자체 제조 역량을 4배로 강화했다.
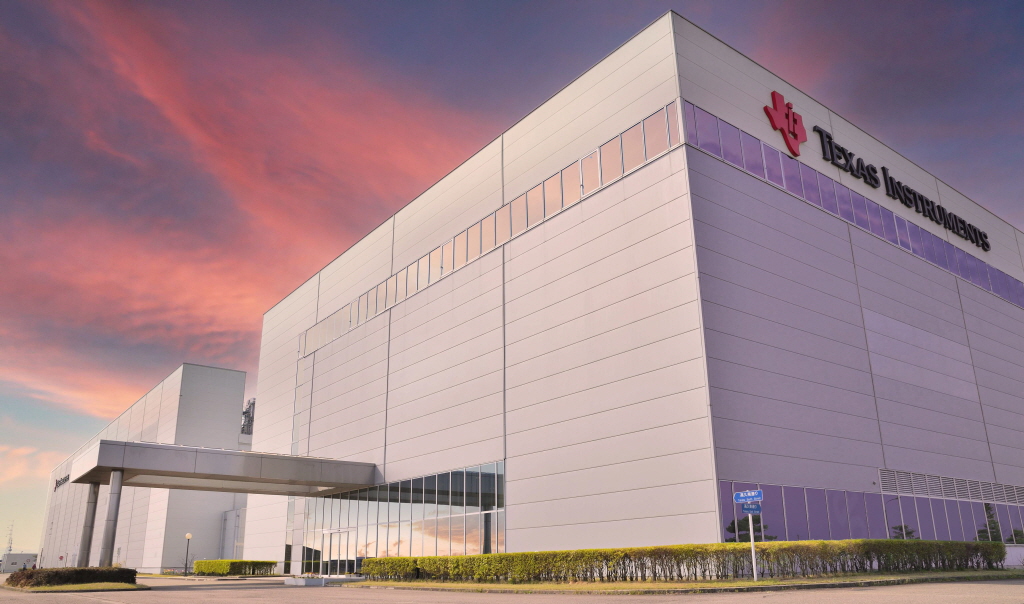
▲텍사스 인스트루먼트(TI) 일본 아이주 팩토리 전경
日 아이주 팩토리 본격 가동, 2030년 내부 제조 95% 이상 확대
텍사스 인스트루먼트(TI)가 일본 아이주 팩토리를 본격 가동하며, GaN(갈륨나이트라이드) 전력 반도체의 자체 제조 역량을 4배로 강화했다.
TI 코리아(대표이사 박중서)는 TI 일본 아이주 제조 시설에서 GaN(질화 갈륨) 기반 전력 반도체 제조를 시작했다고 25일 밝혔다.
미국 텍사스주 댈러스에 위치한 기존 GaN 제조 시설에 이어 아이주 공장이 가동되면서, TI에서 자체적으로 제조하는 GaN 기반 전력 반도체의 제조량이 4 배로 증가하게 된다.
TI의 기술 및 제조 담당 수석 부사장인 모하마드 유누스(Moha㎜ad Yunus)는 “TI가 10년 이상 쌓아온 GaN 칩 설계 및 제조 분야의 전문성을 바탕으로 현재 가장 확장 가능하고 비용 경쟁력 있는 200㎜ GaN 기술을 성공적으로 검증하고 이를 통해 아이주에서 대량 생산을 시작하게 됐다”고 말했다.
또한 그는 “이번 성과를 통해 TI는 2030년까지 내부 제조 비율을 95% 이상으로 확대하면서 더 많은 GaN 칩을 내부에서 제조할 수 있게 됐으며, TI의 여러 공장에서 에너지 효율적인 고전력 반도체로 구성된 전체 GaN 포트폴리오를 안정적으로 공급할 수 있을 것”이라고 밝혔다.
GaN은 실리콘을 대체하는 반도체 소재로 에너지 효율성, 스위칭 속도, 전력 솔루션 크기와 무게, 전체 시스템 비용, 고온 및 고전압 조건에서의 성능 측면에서 장점을 제공한다.
GaN 칩은 더 높은 전력 밀도나 더 작은 공간에서 전력을 제공해야 하는 노트북 및 휴대폰용 전원 어댑터 또는 냉난방 시스템 및 가전제품을 위한 더 작고 에너지 효율적인 모터와 같은 애플리케이션을 지원한다.
TI는 오늘날 가장 에너지 효율적이고 안정적이며 전력 밀도가 높은 전자 제품을 구현하기 위해 저전압에서 고전압에 이르는 가장 광범위한 통합 GaN 기반 전력 반도체 포트폴리오를 제공하고 있다.
TI의 고전압 전력 부문 부사장인 캐넌 사운다라판디안(Kannan Soundarapandian)은 “TI의 GaN 기술은 시장의 주요 요청 사항인 더 작은 공간에서, 더 많은 전력을, 더 효율적으로 제공할 수 있도록 지원한다”고 말했다.
이어 “서버 전력, 태양광 발전, AC/DC 어댑터 등의 시스템 설계자들이 전력 소비를 줄이고 에너지 효율을 향상시켜야 하는 과제에 직면하면서 TI의 고성능 GaN 기반 칩의 안정적인 공급에 대한 요구가 점점 더 커지고 있다. TI의 통합 GaN 전력계 제품 포트폴리오로 고객은 더 높은 전력 밀도, 향상된 사용 편의성, 낮은 시스템 비용을 구현할 수 있다”고 말했다.
특히 TI GaN 반도체는 TI의 독자적인 GaN-온-실리콘(GaN-on-silicon) 공정, 8천만 시간 이상의 신뢰성 테스트, 통합 보호 기능을 바탕으로 고전압 시스템에서 안전하게 유지되도록 설계됐다.
TI는 가장 최신의 첨단 GaN 칩 제조 장비를 사용하여 제품 성능과 제조 공정 효율성을 높이고 비용 면에서도 이점을 제공한다.
또한 TI의 확장된 GaN 제조에 사용되는 보다 발전되고 효율적인 툴은 더 작은 칩에 더 많은 전력을 담을 수 있다. 이와 같은 설계 혁신은 생산 과정에서 물과 에너지, 원자재의 사용량을 줄여 줘 GaN 칩을 사용하는 최종 제품도 이와 같은 환경적 이점에 기여할 수 있다.
더불어 TI는 더욱 강화된 GaN 제조 역량의 이점을 통해 900V를 시작으로 시간이 지남에 따라 더 높은 전압으로 GaN 칩을 확장할 수 있어 로봇 공학, 재생 에너지 및 서버 전원 공급 장치와 같은 애플리케이션의 전력 효율 및 크기 혁신을 더욱 촉진할 수 있다.
뿐만 아니라 TI는 올해 초 300㎜ 웨이퍼에서 GaN 제조 공정 개발을 위한 파일럿을 성공적으로 완료하는 등 투자를 확대하고 있다. 더 나아가 TI는 확장된 GaN 제조 공정을 300㎜ 기술로 완전히 이전할 수 있어 고객의 요구에 따라 쉽게 확장하고 향후 300㎜로 전환할 수 있는 입지를 확보했다.
GaN 기술의 공급 확대와 혁신은 책임감 있고 지속 가능한 제조를 향한 TI의 노력을 보여주는 최신 사례다.
TI는 2027년까지 미국 내 사업장에서 100% 재생 전기를 사용하고, 2030년까지는 전 세계적으로 이를 달성한다는 목표를 가지고 있다.