한국전기연구원(KERI) 나노융합연구센터 한중탁 박사팀이 차세대 이차전지의 친환경 건식 공정(dry process)에 간편하게 적용되는 ‘고분산성 탄소나노튜브(CNT, Carbon Nano Tube) 파우더 제조 기술’을 세계 최초로 개발하며, 응집하려는 성질이 강한 CNT의 효과적인 분산에 성공했다. CNT의 이차전지 건식공정 적용의 길을 열며, 차세대 이차전지 고용량화 실현에 기여할 것으로 기대가 모아진다.
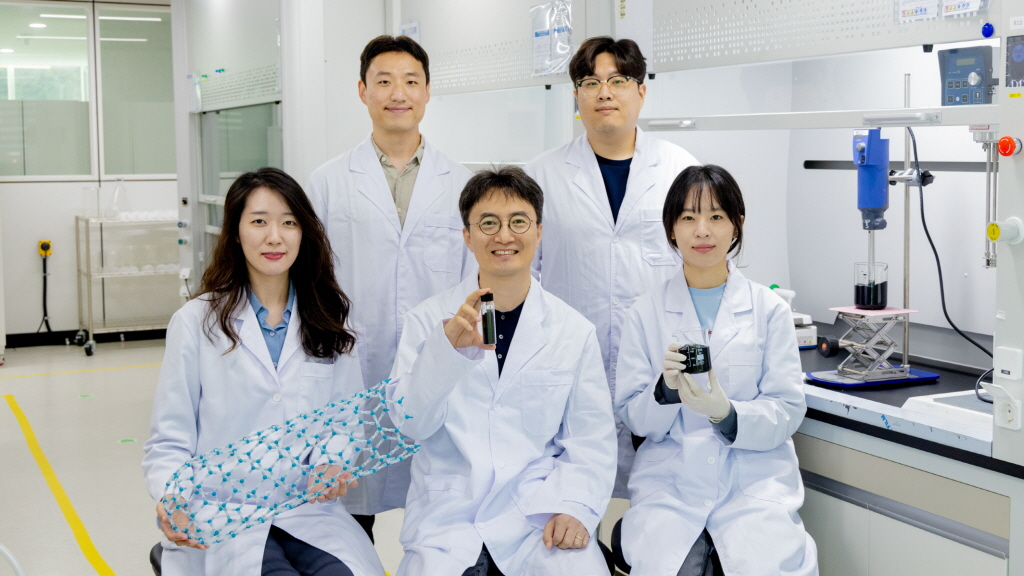
▲KERI 한중탁 박사(앞줄 가운데)를 비롯한 연구팀이 탄소나노튜브(CNT)를 파우더(가루) 형태로 만들어 손쉽게 분산하는 기술을 개발했다.
CNT 파우더 제조 기술, 건식 공정 적용 가능
한국전기연구원(KERI)이 응집하려는 성질이 강한 CNT의 효과적인 분산에 성공하며, CNT의 이차전지 건식공정 적용의 길을 열었다. 차세대 이차전지 고용량화 실현에 기여할 것으로 기대가 모아진다.
KERI는 나노융합연구센터 한중탁 박사팀이 차세대 이차전지의 친환경 건식 공정(dry process)에 간편하게 적용되는 ‘고분산성 탄소나노튜브(CNT, Carbon Nano Tube) 파우더 제조 기술’을 세계 최초로 개발했다고 25일 밝혔다.
CNT는 강철의 100배 강도에, 전기전도도는 구리에 버금가는 수준을 가진 신소재로, 6각형 고리로 연결된 탄소들이 긴 원통형 모양을 이루고 있다. CNT는 기존 이차전지의 도전재로 사용되는 카본블랙에 비해 유연하고 전기전도성이 우수한 1차원 나노 소재다.
CNT가 차세대 이차전지의 도전재로 사용될 경우, 소량의 첨가만으로도 에너지 밀도를 크게 높일 수 있다.
반면에 CNT는 서로 응집하려는 성질이 매우 강해 서로 엉킨 구조를 가지고, 이차전지의 다른 물질인 바인더, 활물질 등과 고루 섞이지 않는다는 문제가 있다.
특히 건식 공정(dry process)의 경우, CNT를 용매가 없는 조건에서 다른 물질과 균일하게 혼합해야 하는 문제점을 안고 있으며, 이는 전지 산업계가 해결해야 할 과제 중 하나로 손꼽혔다.
한중탁 박사팀의 성과는 CNT를 파우더(가루) 형태로 만들어 응집을 최소화해 건식공정에서 활물질이나 바인더 소재와 손쉽게 분산하는 기술을 개발한 것이다. 연구진은 수년간의 연구를 통해 CNT들이 파우더 상태에서도 서로 뭉치지 않고, 떨어진 상태를 유지할 수 있도록 제어하는 데 성공했다.
이를 통해 까다로운 건식 공정에서도 1차원 구조의 긴 CNT로 도전재를 만들어 고용량 전지를 제조할 수 있는 길이 열렸다. 용매 사용 없이도 잘 분산된 고전도성의 CNT는 내부의 다른 물질들을 전기적으로 잘 연결해 줌으로써 차세대 이차전지의 성능을 높이는 데 크게 기여할 수 있다.
KERI 한중탁 박사는 “건식 공정은 유독성의 용매를 사용하지 않아 친환경적이고, 당연히 이를 회수할 필요도 없어 공정이 간소하며, 생산비용도 저렴해 세계적인 전기차 업체에서도 주목한다”며 “건식 공정에서 CNT를 효과적으로 분산해 도전재를 만든 것은 우리가 세계최초이고, 차세대 이차전지 기술의 초격차를 확보하는 데 큰 도움이 될 것”이라고 전했다.
성과와 관련해 국내 특허 출원까지 마친 KERI는 ‘고분산성 CNT 파우더 제조 기술’을 고용량의 두꺼운 후막 음극/양극에도 적용하는 등 다양한 검증을 진행하고 있다.
또한 이번 성과가 차세대 전지로서 건식공정이 필요한 리튬황전지, 전고체전지 등 관련 업계의 많은 관심을 받을 것으로 보고, 수요 기업을 발굴해 기술이전에 나설 계획이다.
한편 KERI는 과학기술정보통신부 국가과학기술연구회 산하 정부출연연구기관이다. 이번 연구는 KERI 기본사업과 국가과학기술연구회 창의형융합연구사업의 지원을 받아 수행됐다.