한국전기연구원(KERI) 스마트3D프린팅연구팀의 설승권 박사팀이 꿈의 신소재로 알려진 ‘맥신(MXene)’을 활용해 고해상도의 3D 미세 구조물을 인쇄하는 기술을 세계 최초로 개발하며, 고효율 배터리나 전자기 차폐 등 다양한 분야에서 활용될 것으로 기대가 모아진다.
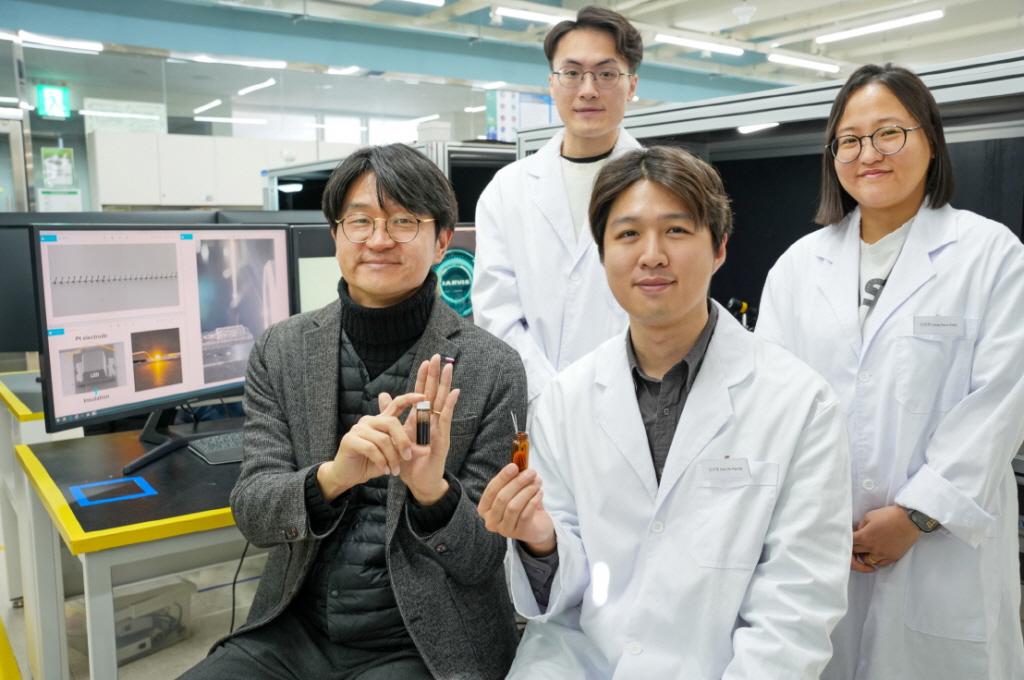
▲KERI 설승권(앞줄 왼쪽) 박사팀이 맥신을 이용한 3D 프린팅용 잉크와 노즐을 들고 포즈를 취하고 있다.
전기연구원, ‘맥신’ 활용 머리카락 굵기 약 1/100 수준 인쇄
높은 전기 전도성과 전자파 차단 능력을 보유하고 있는 ‘맥신’(MXene)을 이용해 머리카락 굵기의 약 1/100 수준의 3D 미세 프린팅에 성공해 향후 고효율 배터리나 전자기 차폐 등 다양한 분야에서 활용될 것으로 기대가 모아진다.
한국전기연구원(KERI) 스마트3D프린팅연구팀의 설승권 박사팀이 꿈의 신소재로 알려진 ‘맥신(MXene)’을 활용해 고해상도의 3D 미세 구조물을 인쇄하는 기술을 세계 최초로 개발했다.
2011년 미국에서 처음 발견된 맥신은 금속층과 탄소층이 교대로 쌓인 2차원 나노 물질이다. 맥신은 높은 전기 전도성과 전자파 차단 능력을 보유하고 있고, 여러 금속 화학물과의 조합이 용이한 특성이 있어 고효율 배터리나 전자기 차폐(shield) 등 다양한 분야에서 크게 주목받고 있다.
반면에 맥신을 3D 프린팅 분야에 적용하려면 별도의 첨가제(바인더)가 필요하며, 인쇄에 맞게 최적의 잉크 점도(농도)로 조절해야 하는 어려움이 있었다. 즉, 맥신의 공급량이 너무 많으면 고농도의 잉크가 피펫 노즐을 막는 문제가 발생했고, 반대로 양을 크게 줄이면 원하는 구조물을 충분히 인쇄하는 데 한계가 나타났던 것이다. 첨가제로 인해 맥신 본래의 성질이 손상된다는 단점도 있었다.
이를 해결하기 위해 설승권 박사팀은 독자적으로 보유한 ‘메니스커스(Meniscus)’ 방식을 활용했다. 메니스커스는 물방울 등을 일정 압력으로 지그시 누르거나 당기면 모세관 현상에 의해 물방울이 터지지 않으면서 외벽에 곡면이 형성되는 현상이다. KERI 연구진은 높은 친수성(親水性)을 보유한 맥신을 바인더 없이 물에 분산시켜 낮은 점도로도 고해상도 미세 구조물을 인쇄할 수 있는 3D 프린팅용 나노 잉크를 제조하는 데 성공했다.
인쇄 원리는 단순하다. 먼저, 3D 프린터 노즐에서 잉크를 분사하면 맥신 등 나노 물질이 메니스커스를 통로로 삼아 뿜어져 나온다. 이때 잉크의 메니스커스 표면에서 물(용매)이 빠르게 증발하고, 내부에 강한 인력(반데르발스 힘)이 작용하여 나노 물질들이 서로 결합하게 된다. 이렇게 노즐을 이동하며 해당 과정을 연속해서 진행하면 전기가 통하는 3D 마이크로 구조물이 탄생하는 원리다.
이번 성과는 첨가제 없이 맥신의 특성을 최대한 활용한 방법으로, 결과물도 뛰어났다. 인쇄 해상도는 기존 기술 대비 무려 270배나 높은 1.3㎛(마이크로미터)로, 머리카락 굵기의 약 1/100 수준이다.
3D 인쇄 구조물의 미세화를 통해 전기·전자 소자의 성능과 활용성도 대폭 커졌다. 배터리 등 에너지 저장 장치 분야에 활용되면, 구조물의 표면적과 집적도를 높여 이온 전달 효율을 극대화하고, 에너지 밀도를 증대시킬 수 있다. 전자기 차폐에서는 내부의 다중 반사와 흡수 효과를 증폭하여 성능을 향상 시킬 수 있다. 그 외에 다양한 센서를 제작할 때도 민감도 증대 및 효율 향상 등을 기대할 수 있다.
설승권 박사는 “맥신 잉크의 농도 조건을 최적화하고, 인쇄 공정에서 발생할 수 있는 다양한 매개변수들을 정밀 분석하는 데 많은 노력을 기울였다”며 “우리의 기술은 별도의 첨가제나 후처리 공정 없이도 맥신의 장점을 살려 고강도·고정밀 3D 마이크로 구조물을 얻을 수 있는 세계 최초의 성과”라고 전했다.
이번 연구 결과는 높은 평가를 받아 독일 와일리(Wiley) 출판사의 재료분야 세계적 학술지인 ‘스몰(Small)’ 표지논문으로 최근 선정(JCR 상위 7%, IF=13)됐다. KERI는 개발 기술의 사업화를 위해 수요 업체를 적극 발굴한다는 계획이다. 또한, 최근 물리적 형태에 구애받지 않는 ‘폼팩터-프리(Form-Factor Free)’ 초소형·유연 전자 장치에 대한 수요가 증가하고 있는 만큼, 나노잉크 기반 3D 프린팅 기술을 통해 관련 시장 분야를 선도한다는 목표다.
한편, KERI는 과학기술정보통신부 국가과학기술연구회 산하 정부출연연구기관이다. 이번 연구는 KERI 기본사업 및 과기부 ‘인간-로봇 실시간 상호작용 가능 휴머노이드 골격 맞춤형 3D인쇄회로기판 소재 및 공정 기술 개발’ 과제로 진행됐다. 설승권 박사는 과학기술연합대학원대학교(UST) KERI 캠퍼스 교수로도 활동하고 있다.
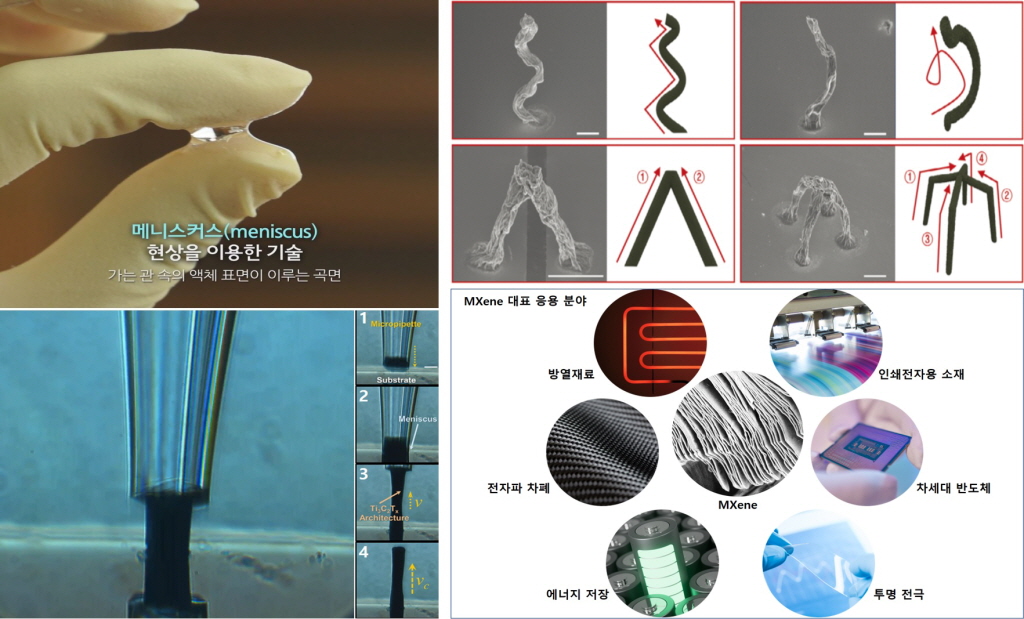
▲메니스커스를 활용한 '맥신 잉크 기반 3D 프린팅' 장면(왼쪽), 이로 인한 결과물 및 활용 분야(오른쪽)