지멘스가 실현가능한 디지털 트윈 솔루션(xDT)을 통해 배터리 소재부터 완제품까지 성능과 수명을 예측해 배터리 안정성을 사전 검증할 수 있다고 주장했다. 지멘스는 파트너들과 모든 공정 과정을 아우르는 지속가능한 배터리 제조 생태계를 구축하겠다는 포부를 드러냈다.
▲지멘스 오병준 한국지사장
전기차 대중화…배터리 에너지 효율성 제고
엑셀러레이터, 디지털트윈·자동화·생성형 AI 솔루션
지멘스-LG에너지솔루션·토요타·보쉬 파트너십 확대
지멘스가 실현가능한 디지털 트윈 솔루션(xDT)을 통해 배터리 소재부터 완제품까지 성능과 수명을 예측해 배터리 안정성을 사전 검증할 수 있다고 주장했다. 지멘스는 파트너들과 모든 공정 과정을 아우르는 지속가능한 배터리 제조 생태계를 구축하겠다는 포부를 드러냈다.
지멘스가 15일(금) 엘타워 오르체홀에서 '지멘스 배터리 데이(Siemens Battery Day)'와 함께 기자간담회를 개최해 지멘스의 배터리 전략과 배터리데이 2024 관련 소식에 대해 전했다. '지멘스 디지털 인더스트리 소프트웨어(DISW)'가 진행한 행사에는 오병준 한국지사장, 푸니트 시나(Puneet Sinha) 배터리 산업 글로벌 총괄 겸 선임 이사, 티노 힐데브란트(Tino Hildebrand) 한국지멘스 선임 부사장 겸 지멘스 디지털 인더스트리(DI) 부문장이 참석했다.
전기차 시장이 성장하며 수요가 급증한 배터리는 산업별 요구사항에 맞는 빠른 시장 출시가 중요해졌다. 배터리 제조사는 지속 가능성, 소재, 효율적 설계, 수명 단축, 재사용/재활용 등 배터리의 전 수명주기를 고려하고, 배터리 정보를 담고 있는 '배터리 여권'과 같은 규제를 달성해야 하는 문제에 직면해있다.
특히 배터리 업계는 배터리 생산 효율성 제고에 방점을 둔다. 푸니타 선임 이사는 "전기차가 대중화되기 전 에너지 효율화와 비용 문제는 풀어야 할 숙제다. 에너지 밀도를 2배 정도 높이고, 비용은 50%를 줄여야 한다"고 말했다. 또한 "스크랩의 발생 비율도 신생 기업의 경우 40%, 오래된 기업이더라도 10%에 육박해 대량생산 시 비효율적이다"라고 지적했다.
지멘스는 해결 방안으로 '디지털 트윈'을 제시한다. 디지털 트윈은 3D 가상세계와 현실세계를 결합하는 개념으로, 배터리 제품, 장비, 공장 등을 가상으로 설계 및 시뮬레이션을 통해 최적화를 달성한 후 이를 현실에 적용하는 기술이다. 지멘스의 '엑셀러레이터(Xcelerator)'은 디지털 트윈, 자동화 기술, 생성형 AI를 기반으로 고객의 디지털 전환을 돕는 통합 솔루션이다.
특히 지멘스는 디지털 트윈 개념을 넘어 'xDT(Executable Digital Twin, 실현가능한 디지털 트윈)'를 강조한다. xDT는 분자 단계에서 시스템 단계에 이르는 배터리의 성능과 수명을 예측하고, 실시간으로 시뮬레이션 함으로써 공정을 검증한다는 개념이다.
기존의 솔루션이 원타임(One-time) 시뮬레이션으로 최적화 결과를 획득하는 단방향 디지털 트윈인 반면, xDT는 지속적으로 제조 데이터를 실시간 수집 및 분석해 예측하는 바를 즉시 적용해 공장을 제어하고, 문제를 해결하는 양방향 디지털 트윈이다. xDT는 배터리, 드론, 로봇 공정 등에서 적용되고 있다.
배터리 제조 시 디지털 트윈 기술을 통해 온도에 따른 성능 변화를 예측하고, 배터리 열폭주 위험성을 낮춰 전기차 안전성을 강화할 수 있다. 지멘스 오병준 지사장은 "현대차 배터리 성능 개발실 및 팩 설계 시뮬레이션에 지멘스 솔루션이 자주 사용되고 있다. 시뮬레이션으로 배터리 열폭주를 5분에서 최대 30분으로 늦추거나, 또는 휘발유 물질을 폭발 전 내부에 가두는 기술이 개발되고 있다"고 말했다.
또한 디지털 트윈 솔루션으로 배터리의 수명을 파악할 수 있다. 실제 차량을 검증하지 않고, 시뮬레이션 차량에서 배터리의 10년 후 성능을 예측해 데이터를 획득할 수 있고, 차량 업체에게 실제 정보를 전달받아 시뮬레이션 결과와 통합 및 비교하여 성능 저하 요인을 발견할 수 있다는 설명이다. 오 지사장은 "배터리 수명 측정 분야에 많은 회사들이 투자하고 있고, 수명이 다한 데이터라도 다시 활용되도록 연구 중이다"라고 말했다.
그러나 배터리 수명 예측은 가장 어려운 부분이다. 오 지사장은 "최근 화두인 보급형 배터리 'LFP(리튬인삼철배터리)'의 겨울철 성능 저하 문제 등에서 배터리뿐만 아니라 환경적 영향을 포함한 다양한 요인이 다양하게 영향을 주기 때문에 자동차의 실제 정보를 함께 비교해 데이터를 수집 및 분석하는 것이 중요하다"고 덧붙였다.
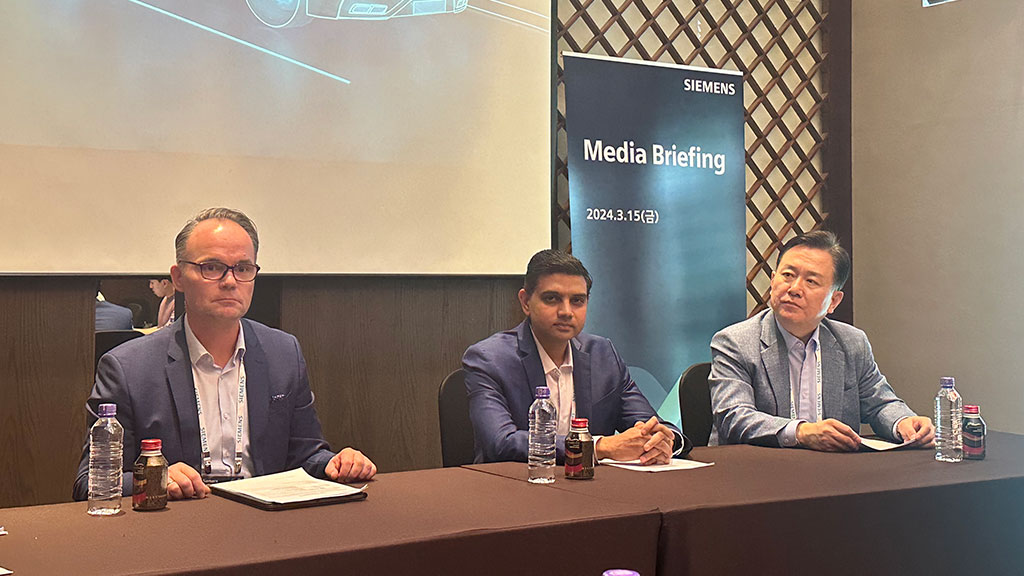
▲티노 힐데브란트 선임 부사장, 푸니트 시나 선임이사, 오병준 지사장
티노 부사장은 "지멘스의 디지털 트윈 솔루션은 배터리 생산 시 지속 가능성을 주축으로 두고, 현실에 유연하게 대응하며 범위를 확대하고(scale-up), 혁신 기술의 청사진을 파트너들과 공유하며 제조 단계를 가속화할 수 있다"고 말했다.
지멘스는 지속 가능성을 핵심 전략으로 꼽는다. 지멘스는 배터리 산업 생태계 내 업체들이 지멘스의 솔루션으로 협업하며 배터리 설계부터 완제품까지 모든 단계에 지속 가능성이 녹아 들어야 한다는 점을 강조한다. 디지털 트윈 전략으로 엔지니어링의 자원, 전력 등을 최적화하는 방법도 한 부분이다.
오 지사장은 "배터리 셀을 적층하는 대용량 배터리 장비인 '스태킹(Stacking) 장비'를 납품받아 설치해서 생산하는 데 3개월이 걸렸지만, 디지털 트윈으로 사전에 장비가 어떻게 작동할 지 검증하면 약 30% 이상의 시간을 절약할 수 있다"며, "지멘스의 지속 가능성은 3달에서 2달로 생산 및 납품 시간을 단축하고, 지멘스 솔루션을 활용하는 고객들도 지속 가능성에 기여할 수 있게 하는 전략"이라고 덧붙였다.
지멘스는 컨설팅, 설계, 엔지니어링, 자동화, SW, 규제, 인증, 보안, 물류에 이르는 엔드 투 엔드(End-to-End) 솔루션을 제공한다. 푸니트 선임이사는 "배터리 산업은 배터리 생산업체, 에너지 업체, 전력 저장업체, 자동차 제조 업체, 장비 업체 등 다른 공정과 다르게 화학, 기계, 조립산업 등 모든 영역이 합쳐져 있고, 실제 실험으로 검증하기 어려운 부분이 많아 자동차 기업들의 협업이 중요하다"며, 파트너들과의 상생을 강조했다.
이를 위해 지멘스는 '디지털 스레드(Digital Thread)'에 주안점을 두고 있다. 디지털 스레드는 지멘스의 엔드 투 엔드 솔루션의 연결 관계와 상호 이동되는 데이터를 정의한 템플릿을 뜻한다. 지멘스의 고객들은 자사의 공정 라인에 다양한 솔루션을 도입할 때, 해당 템플릿을 통해 쉽게 통합할 수 있다. 지멘스의 고객사 LG에너지솔루션은 탱크 안의 믹서 장비들을 버추얼 센서로 모니터링 및 제어할 수 있는 솔루션의 도입을 검토하고 있다.
한편 지멘스는 LG에너지솔루션, 노스볼트(nothvolt), 토요타(TOYOTA), 보쉬(BOSCH) 등을 비롯해 글로벌 배터리 제조사와 파트너십을 맺고 있다. 예컨대 팩 엔지니어링 기업 '푸조(PEUGEOT)'는 가상 현실에서 시제품을 제작해 엔지니어링 시간을 50% 줄였다. 신생업체 '프레이(FREY)'는 스마트팩토리 구현을 위해 IT와 OT를 융합해 공장을 자동화했다. 또한 아시아 배터리 공급업체 ‘Voltaiq’는 배터리 폐기율을 과거 대비 10%로 줄였다. 푸니트는 “지멘스의 솔루션 도입 시 1년에 1억달러 정도의 비용을 절감할 수 있다”고 말했다.