인피니언 테크놀로지스가 공급하는 CoolSiC™ 기술과 CoolSiC™ 제품에 대해 인피니언의 엔지니어들이 자세히 소개한다.
인피니언 SiC 기술, 칩은 작고 성능은 최대
트랜치 디자인, 작은 다이크기 소재 최대 활용
디스크리트·모듈 패키징, 열적 성능 최대 상승
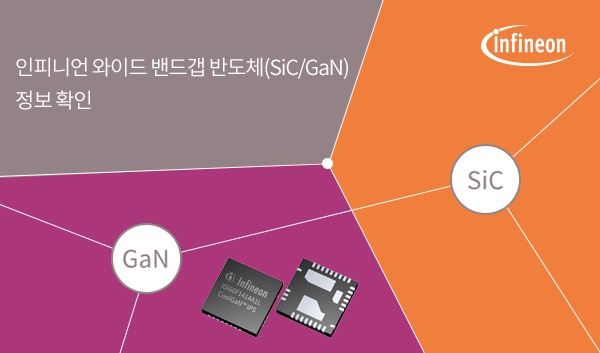
■ 지속가능 에너지 시대, SiC 전력 반도체 수요 급상승
전세계적으로 에너지 수요가 계속해서 증가하고 있다. 사람들이 날마다 엄청난 양의 디지털 콘텐츠를 소비하고, 전자 기기들을 클라우드로 연결하고, 자동차 전기화가 가속화되는 것 모두가 에너지 수요를 빠르게 증가시키는 요인이 되고 있다.
한편으로 탄소 배출을 줄이고 에너지를 지속가능하게 생산하고 소비해야 하는 요구가 높아지고 있다.
이러한 요구를 충족할 수 있는 한 가지 방법이
실리콘 카바이드(SiC) 전력 반도체를 사용해서 효율이 우수한 전력 변환 디자인을 설계하는 것이다.
시장에는 이미 SiC를 적용한 전력 반도체가 다양하게 출시돼 있다. SiC의 기본적인 장점은 더 높은 스위칭 주파수가 가능하고, 높은 효율을 달성하고, 열 발생을 줄인다는 것이다. 이것은 시스템 비용을 절감하는 것으로 이어진다. 이 글에서는 높은 효율의 SiC 디자인을 달성하기 위해서 고려해야 할 세 가지 측면에 대해서 설명한다.
■ 디바이스 디자인 - 트렌치 SiC MOSFET의 선구자
인피니언은 트렌치 SiC MOSFET 기술의 선구자로서 1990년대에 벌써 최초로 이 기술을 발표했다. Si-MOS 기술의 한계와 가능성에 대한 축적된 노하우를 바탕으로 트렌치 기반 디바이스 디자인을 고안했다(그림 1). 트렌치 SiC MOSFET은 신뢰성을 해치지 않으면서 온(on) 상태 저항이 낮다는 점이 장점이다. 대체로 트렌치 기반 수직형 전력 디바이스는 특정한 성능대로 작은 다이 크기로 소재를 최대한 활용하도록 한다. 이것은 기존에 실리콘 기반 전력 스위치로 확인되었으며, SiC 디바이스로는 특히 더 중요하다. SiC는 소재 자체가 큰 비용 요인이기 때문이다.
또한 트렌치 기반 디바이스로 SiC 결정의 고유한 물리적 특성에 의해서, 게이트 산화막으로 안전한 동작 전계를 유지하기만 한다면 평면형 디바이스보다 면적당 더 낮은 저항을 달성할 수 있다. 그러므로 트렌치 MOSFET 디자인은 신뢰성과 뛰어난 성능을 결합할 수 있다. 그 밖에 또 다른 이점으로서 충분히 높은 임계 전압이 가능하고, 단락 회로 견고성을 조절 가능하고, 애버랜치 정격이 뛰어나고, 커패시턴스 비가 좋으므로 손실이 낮으면서 견고하고 단순한 컨버터 디자인을 설계할 수 있다.
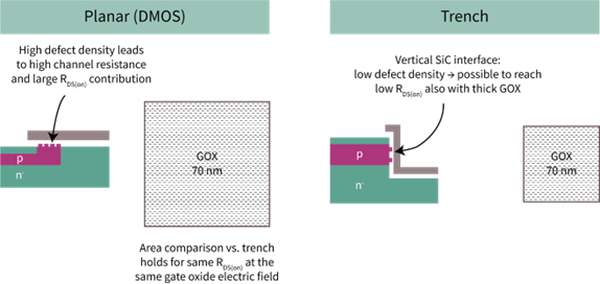
▲그림 1 : 평면형과 트렌치 MOSFET 구조 비교
디바이스 디자인에 있어서 또 다른 특징은, SiC MOSFET으로 진성 바디 다이오드를 통합함으로써 외부에 고속 프리휠링 다이오드가 필요하지 않다는 것이다. 인피니언의
CoolSiC™ MOSFET은 바디 다이오드를 최대한 활용해서 하드 커뮤테이션 시에 견고성을 높이고 역 복구 전하를 낮춘다. 기술적 조치들과 품질 검사를 통해서 능동 바디 다이오드 동작이 심한 드리프트를 일으키지 않도록 한다.
트렌치 기반 SiC MOSFET은 높은 임계 전압을 사용할 수 있으며 전류 턴오프 시에 신호대 잡음비에 있어서 새로운 기준을 제시한다. 이 점은 시스템 차원에서 Si MOSFET과 유사하게 제로 게이트 전압 턴오프를 구현하기 위해서 중요하다. 제로 전압 턴오프는 음의 구동 전압을 필요로 하지 않으므로 게이트 구동을 간소화한다. 그러므로 부품 수를 줄이고 복잡성을 낮추므로 시스템 신뢰성을 높이는 것으로 이어진다.
그런데 제로 전압 턴오프는 원치 않는 기생 턴온을 발생시킬 수 있다. MOSFET은 커패시턴스 분배기로 표현할 수 있으므로, 어떠한 드레인-소스 전압 변화는 게이트-소스 전압 변화로 이어진다. 만약에 게이트-소스 전압이 MOSFET 임계 전압보다 높으면 MOSFET이 약하게 턴온할 수 있다. 이것은 턴온 손실을 증가시킨다.
CoolSiC™ MOSFET은 다음과 같은 조치들을 통해서 기생 턴온에 대한 견고성을 높이도록 설계됐다.
- 임계 전압을 높였다. 인피니언의 CoolSiC™ 기술은 임계 전압에 있어서 새로운 기준을 제시한다.
- 커패시턴스 비를 최적화함으로써 드레인-소스 전압 변화로 인해서 결합되는 원치 않는 전압을 최소화하도록 했다.
인피니언의 트렌치 기술은 낮은 온(on) 저항에다 단락 회로 견고성을 결합했다. CoolSiC™ MOSFET 제품은 제품 구성에 따라서 최대 3μs에 이르는 단락 회로 견딤 시간이 가능하다. 드라이브 타입 애플리케이션은 견고한 단락 회로 성능을 중요하게 요구한다. 그림 2에서는 1200V 디스크리트 MOSFET의 단락 회로 동작을 보여준다. 경우에 따라서 지정된 단락 회로 견딤 시간을 충족하기 위해서 추가적인 조치가 필요할 수 있다. 인피니언은 제품 출하에 앞서서 모든 제품에 대해서 지정된 단락 회로 견딤 시간으로 100퍼센트 생산 테스트를 실시한다.
.jpg)
▲그림 2 : 인피니언의 1200V CoolSiC™ MOSFET의 단락 회로 동작(소스 검출 핀이 있는 패키지와 없는 패키지)
■ 칩과 패키지 사이의 시너지 작용
실리콘(Si) 칩에 비해서 SiC 기반 칩은 크기를 더 작게 할 수 있다. 인피니언은 열 성능과 전력 취급 용량 사이에 절충이 필요할 수 있는 문제를 완화하기 위해서 정교한 인터커넥트 기술을 적용해서 소재를 최대한 활용하도록 했다. 그럼으로써 CoolSiC™ 칩 기술은 디스크리트 및 모듈 패키징으로 열 성능을 끌어올리도록 한다.
디스크리트 디바이스로 확산 솔더링 기법을 사용한다. 확산 솔더링의 가장 큰 장점은 디바이스의 열 임피던스를 크게 낮출 수 있다는 것이다. 통상의 다이 접착 기술은 칩과 패키지 사이에 솔더 층을 사용하는데, 새로운 기법은 다이 후면으로 특수한 금속 층을 적용해서 기계적 및 열적 접속을 형성한다(그림 3).
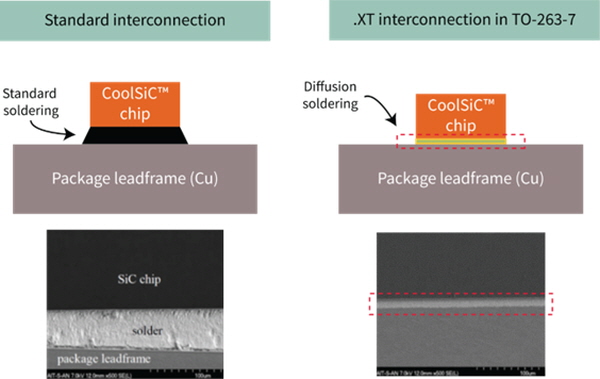
▲그림 3 : 표준 솔더링(왼쪽)과 비교해서 .XT 인터커넥트는 확산 솔더링을 사용해서 솔더 접합부를 거의 제거할 수 있다.
열 임피던스를 낮춤으로써 더 높은 전력 밀도가 가능해진다. 정적 값(RthJH)은 25퍼센트 향상되고, 열 임피던스(ZthJH)는 10ms에 약 50퍼센트의 향상을 나타낸다.
확산 솔더링의 또 다른 장점은 애플리케이션 차원에서 신뢰성을 높인다는 것이다. 특정한 총 손실로 표준 솔더링을 사용할 때보다 디바이스가 더 낮은 온도로 동작할 수 있으므로 본드 와이어 들뜸 같은 결함을 줄일 수 있으며 그러므로 더 높은 사이클링 안정성을 달성할 수 있다.
모듈 패키징은 디스크리트 디바이스와 또 다르다. SiC 칩 특성에는, 인피니언이 수십 년 전에 개발한 것으로서 베이스플레이트를 없앤 EasyPACK™ 플랫폼 같이 유연한 핀 기반 구성이 적합한 것으로 드러났다.
인피니언의
EasyPACK™ 모듈은 토폴로지와 내부 레이아웃이 매우 유연하며, 밀집된 그리드 어레이와 함께 고도로 신뢰할 수 있는 핀 리벳 커넥터 시스템을 제공한다. 그러므로 게이트 루프와 전원 루프로 인덕턴스를 낮춘다. 이 점은 다층 PCB에 모듈을 탑재할 때 중요하다(그림 4).
모듈의 열 성능 또한 중요하다. EasyPACK™ 모듈은 이것을 접합부 대 히트싱크 열 저항(RthJH)으로 나타낸다. 인피니언은 최근에 질화알루미늄(AIN) 세라믹을 적용한 EasyPACK™ 모듈을 출시했다. 이 모듈 제품은 기존 소재와 비교해서 RthJH가 40퍼센트 더 낮다. 열에 있어서 이와 같은 이점은 시스템 차원의 이점으로 이어진다.
그림 5에서는 기존 EasyDUAL™ 11mΩ/1200V 하프브리지 모듈과 AIN 제품을 비교해서 보여준다. AIN 제품으로 접합부 온도를 20K까지 낮추거나 또 다르게는 출력 전류를 30퍼센트까지 높일 수 있다는 것을 알 수 있다.
접합부 온도가 낮아지면 효율을 높일 뿐만 아니라 전력 사이클링과 관련해서 수명을 연장할 수 있다. 반면에 더 높은 출력 전류는 더 높은 출력 전력 정격을 가능하게 한다.
■ 제조 노하우
인피니언의 제조 설비는 Si와 SiC 칩 제조를 대량으로 유연하게 할 수 있도록 설계되었으며, 디스크리트 패키지나 모듈 패키지로 어셈블리도 가능하다. 이것은 CoolMOS™나 TRENCHSTOP™ IGBT 같은 향상된 Si 디바이스 기술의 성공적인 양산을 통해서 입증되고 있다. 2001년 이후부터는 실리콘 전력 기술에 사용되는 것과 동일한 장비와 품질 공정을 사용해서 상용화 SiC 디바이스를 대량으로 생산하고 있다.
안정적인 공정 프로세스와 불량률 제로 전략이 성공적인 양산을 위해서 핵심적 역할을 하고 있으며 고객들도 이 점을 높이 사고 있다. 인피니언은 에피택시 성장이나 첨단 패키징 같은 핵심 기술을 자체적으로 보유하고 있다. 현장에서 오랜 기간에 걸쳐서 축적된 경험을 바탕으로 생산 단계에서뿐만 아니라 현장에 나가서까지 품질을 보장하기 위한 견고한 품질 보장 절차들을 개발했다. 또한 최근에 인피니언은 SiC가 주류로 자리잡도록 하기 위한 큰 걸음으로서 오스트리아와 말레이시아 공장에 와이드 밴드갭(WBG) 생산 용량을 증설하기 위해서 20억 유로를 투자한다고 발표했다
■ 인피니언, 고객 요구 충족 SiC 제품 제공
SiC가 틈새 기술에서 주된 전력 반도체 소재로 자리잡고 있다. 인피니언은 이 시장에서 축적된 경험과 깊이 있는 제조 노하우를 바탕으로 뛰어난 칩 성능을 달성하고 있다. 이 글에서는 높은 효율의 SiC 디자인을 달성하기 위해서 고려해야 할 세 가지 측면에 대해서 설명했다. 인피니언은 선구적인 트렌치 기술을 적용한 디바이스 디자인, 칩과 패키지 사이의 시너지 작용, 축적된 제조 역량을 바탕으로 신뢰성, 유연성, 시스템 성능에 대한 고객들의 요구를 충족하는 SiC 제품을 제공한다. 그럼으로써 SiC의 밝은 미래를 기대하게 한다.
여기에서 인피니언의 CoolSiC™ 기술과 CoolSiC™ 제품에 관한 더 자세한 정보를 볼 수 있다.
※ 저자
- Eva Gabriel, Senior Manager, Product Marketing SiC
- Dr. Zhihui Yuan, Director, Technical Marketing SiC discretes
- Andre Lenze, Senior Staff Engineer, SiC low- and medium power modules
인피니언 테크놀로지스