한국재료연구원(KIMS, 원장 최철진) 금속재료연구본부 알루미늄연구실 어광준, 손현우 박사 연구팀이 내구성을 획기적으로 향상한 전기차용 알루미늄 합금을 개발하는 데 성공해 향후 전기차 사고 위험성을 낮추는데 크게 기여할 것으로 기대된다.
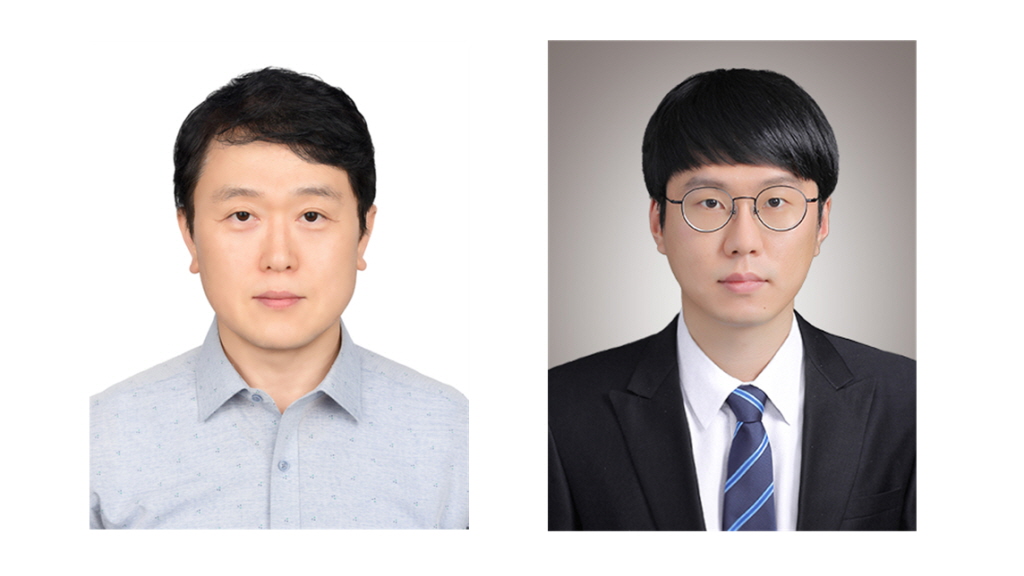
▲이번 연구를 주도한 한국재료연구원 어광준 박사, 손현우 박사(왼쪽부터)
재료연, 전기차용 알루미늄 합금 소재 개발
열적 내구성을 획기적으로 향상한 전기차용 알루미늄 합금 소재가 개발 돼 향후 전기차 사고 위험성을 낮추는데 크게 기여할 것으로 기대된다.
한국재료연구원(KIMS, 원장 최철진)은 금속재료연구본부 알루미늄연구실 어광준, 손현우 박사 연구팀이 내구성을 획기적으로 향상한 전기차용 알루미늄 합금을 개발하는 데 성공했다고 9일 밝혔다.
연구팀은 알루미늄 합금 내부의 나노구조가 작동하는 새로운 메커니즘을 규명하고 이를 통해 개발한 합금이 해외 선진사 소재와 비교해 열적 내구성이 최대 140% 향상됐음을 확인했다.
기존 알루미늄 재질의 배터리 외장재는 배터리가 발산하는 열에 의해 지속해서 열화해 전기차가 노후화할수록 사고 위험성을 치명적으로 높이는 문제가 있었다. 이번에 개발한 알루미늄 합금은 기존 6000계열 알루미늄 합금에 다양한 미량 원소를 첨가해 열적 내구성을 높이고, 발열로 인한 외장재 열화 현상을 지연시킬 수 있다.
연구팀은 투과전자현미경, 3차원 원자탐침현미경을 이용한 최첨단 나노구조 정밀분석 과정을 통해 수십 가지의 미량 원소를 첨가 및 나노구조를 분석해 데이터베이스를 새롭게 구축했다.
이를 기반으로 몇 개의 원소가 열 안정성을 향상할 수 있음을 확인할 수 있었다.
열적 내구성 향상 기술이 적용된 알루미늄 합금은 전기차 배터리 외장재나 초음속 항공기 구조재료 분야 등 고온 환경에서 장시간 사용하는 부품에서 매우 우수한 특성을 발휘할 수 있다.
기존의 열적 내구성 향상 기술은 알루미늄 합금에 오랫동안 사용되어 온 원소의 데이터베이스를 활용하는 한계가 있었다.
이번 연구는 열적 내구성 향상 기술의 데이터베이스를 다각화하고, 새로운 합금 설계 방향을 제시했다는 측면에서 그 의미가 크다.
전기차 배터리 외장재 시장은 2020년 4억6,490만달러에서 연평균 8.4% 성장해 2029년 8억6,330만달러에 달할 것으로 전망된다.
현재 해외 선진사에 비해 기술 경쟁력 측면에서 뒤처지고 있으나, 본 기술을 통한 국산화로 수입 대체 효과는 물론 수출도 가능할 것으로 기대된다.
연구를 주도한 재료연 손현우 박사는 “이번에 개발한 기술이 상용화될 경우, 해외 선진사 대비 뒤처져 있는 고부가가치 알루미늄 합금 개발의 필요성을 인식시키고 이와 함께 국내업체가 좀 더 적극적으로 연구개발 시장에 진입하게 만드는 계기가 될 것”이라고 말했다.
이번 연구성과는 과학기술정보통신부의 지원을 받아 한국재료연구원 기본사업과 국가연구실(N-Lab.) 사업을 통해 수행됐다. 또한 연구결과는 현재까지 SCI급 논문을 3편 게재하고, 관련 특허 2건을 출원한 바 있다. 연구팀은 열 안정성이 우수한 알루미늄 합금 제조 기술의 기초 연구를 마무리하고, 응용 연구를 통해 기술 성숙과 더불어 국내 알루미늄 배터리 외장재 제조업체에 기술을 이전하는 것을 목표로 후속 연구를 진행 중이다.