고전압 디지털 제어 애플리케이션으로 안전한 절연과 낮은 전력 소모를 위한 방법에 대해 인피니언 테크놀로지스 기술진에게 들어봤다.
“ISOFACE™ 디지털 아이솔레이터, 절연 요구 시스템 솔루션 만족”
낮은 전류 소모·향상된 공통 모드 트랜지언트 내성·높은 전달 지연 정확도
고전압 디지털 제어 애플리케이션용으로 견고·신뢰할 수 있는 솔루션 제공
■ 누설 전류 방지, 효과적 갈바닉 절연 중요
고전압 애플리케이션으로 접지 전위가 다른 두 시스템 부분 사이에 원치 않는 누설 전류가 흐르는 것을 막기 위해서 효과적인 갈바닉 절연이 중요하다.
그림 1의 왼쪽은 입력에서 출력으로 DC 리턴 전류가 두 접지 사이에 전위 차이를 일으킴으로써, 신호 무결성을 떨어트리고 품질 저하를 일으킬 수 있다.
이럴 때 아이솔레이터(절연형 게이트 드라이버 IC[2] 또는 디지털 아이솔레이터)가 중요한 역할을 한다.
그림 1의 오른쪽은 이것을 보여준다. 아이솔레이터가 두 회로 부분 사이에 DC 및 통제되지 않은 AC 전류를 차단하고 통신 신호와 전원만 절연 벽을 통과하도록 한다.
아이솔레이터는 고전압 시스템을 취급하는 작업자들을 위해서 필요한 안전 보호 기능을 제공할 뿐만 아니라, 각기 다른 전원 전압 수준으로 동작하는 시스템들 사이에 상호작용이 가능하도록 레벨 쉬프트 기능을 할 수도 있다.
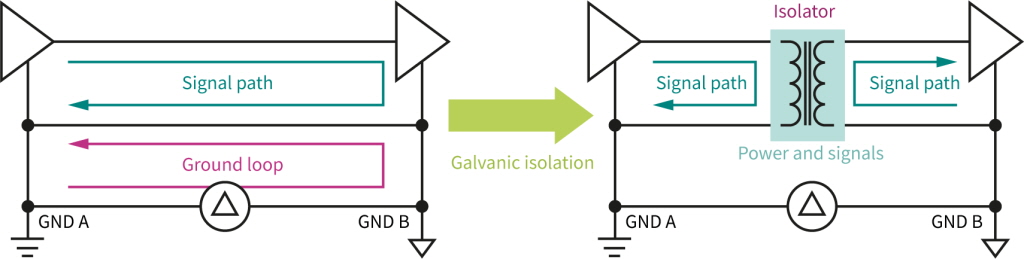
▲그림 1 : 두 시스템 부분 사이에 흐르는 DC 리턴 전류가 원치 않는 접지 루프를 발생시킨다(왼쪽). 갈바닉 절연은 접지 연결을 끊음으로써 원치 않는 접지 루프가 발생되지 않도록 한다(오른쪽).
아이솔레이터는 크게 두 타입으로 구분할 수 있다. 광학적 아이솔레이터와 디지털 아이솔레이터이다.
광학적 아이솔레이터는 흔히 옵토커플러라고 하는 것으로서, 빛을 사용해서 절연 벽을 통해서 신호를 전달하는 아날로그 절연 제품이다. 광학적 아이솔레이터는 예전부터 시장에서 기반을 잡았고 가격적 경쟁력이 뛰어나다는 점에서 수십년 전부터 산업 분야에 널리 사용되어 왔다.
하지만 LED의 스위칭 속도가 달성 가능한 데이터 레이트를 불과 초당 수 메가비트로 제한한다.
뿐만 아니라 광학적 아이솔레이터는 적절한 바이어싱과 LED 구동을 위해서 보드 상으로 추가적인 회로 부품들을 필요로 한다.
그럼으로써 추가적인 PCB 면적을 차지하고 애플리케이션의 BOM(bill of materials)을 증가시킨다.
PCB 면적을 최소화하고 높은 데이터 레이트를 달성하기 위해서 외부적 바이어싱과 구동 회로를 단일 패키지로 통합하는 기법들이 나와 있기는 하나, 이러한 솔루션은 가격이 비싸다.
반면에 디지털 아이솔레이터는 용량성 절연 또는 자기 절연 기술을 사용해서 절연 배리어를 통해서 신호를 전달한다. 이들 기술은 절연 소자의 크기를 크게 줄이고 수명을 연장한다[3].
광학적 아이솔레이터와 비교해서 다음과 같은 이점들에 있어서 최근에 많은 애플리케이션으로 디지털 아이솔레이터가 선호되고 있다.
- 시스템 BOM 최적화 및 PCB 면적 감소
- 정확한 타이밍 특성과 낮은 전력 소모
- 향상된 공통 모드 트랜지언트 내성(CMTI)
- 부품 차원 표준 IEC 60747-17에 따른 절연 수명 보장
- 입력 필터, 트랜시버(CAN, RS-485 등), 출력 인에이블 옵션 같은 추가적인 기능 통합
표 1은 광학적 아이솔레이터와 디지털 아이솔레이터의 차이점을 요약해서 보여준다.
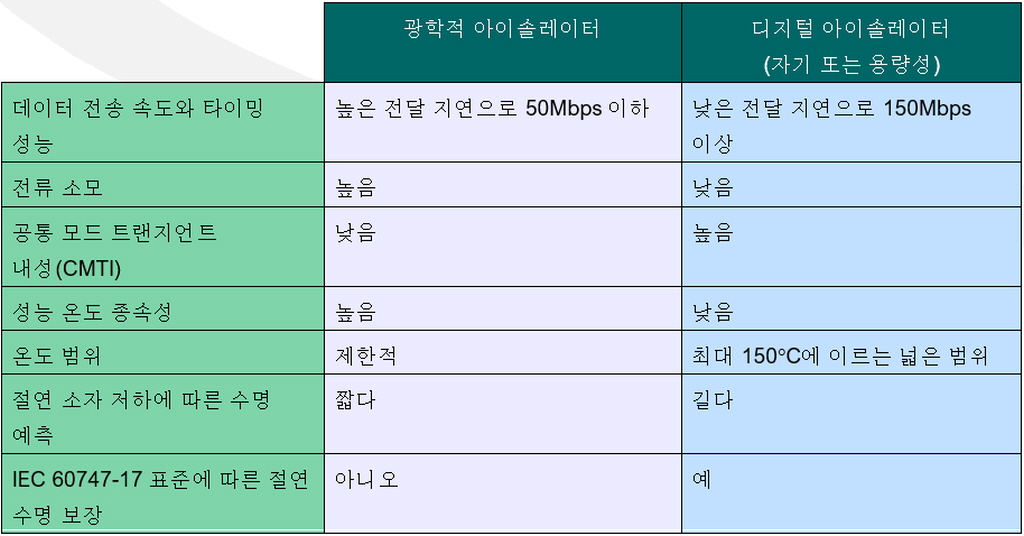
▲표 1 : 광학적 아이솔레이터와 디지털 아이솔레이터의 차이점
■ 인피니언의 1세대 ISOFACE™ 디지털 아이솔레이터 2DIBx4xxF
산업용 애플리케이션으로 갈수록 높아지는 절연 요구를 충족하기 위해서 인피니언은 1세대
듀얼 채널 디지털 아이솔레이터 제품군을 출시했다. 이들 제품은 높은 견고성, 정밀한 타이밍 성능, 낮은 전력 소모를 특징으로 한다.
이들 제품은 인피니언언의 특허 기술인 코어리스 트랜스포머(CT) 기술을 적용했다. 이 혁신 기술은 반도체 제조 프로세스를 사용해서 금속 나선으로 이루어진 온칩 트랜스포머를 내부로 통합하고 실리콘 다이옥사이드(SiO2) 절연 벽으로 분리를 한다(그림 2). 이 접근법은 절연 벽의 트랜스포머를 통해서 입력과 출력 사이에 신호를 전달한다.
▲그림 2 : 인피니언의 ISOFACE™ 디지털 아이솔레이터 2DIBx4xxF 제품에 사용된 코어리스 트랜스포머의 단면도
뿐만 아니라 글리치 필터, 통신 변조, 워치독, 저전압 록아웃(UVLO) 같은 기능들을 포함함으로써 높은 전압과 잡음이 존재하는 까다로운 산업용 환경으로도 견고하고도 신뢰할 수 있는 데이터 전송을 가능하게 한다.
표 2는 각기 다른 채널 구성, 페일 세이프 디폴트 출력 상태, 가변 또는 고정 입력 한계로 이 제품군의 제품들을 보여준다.
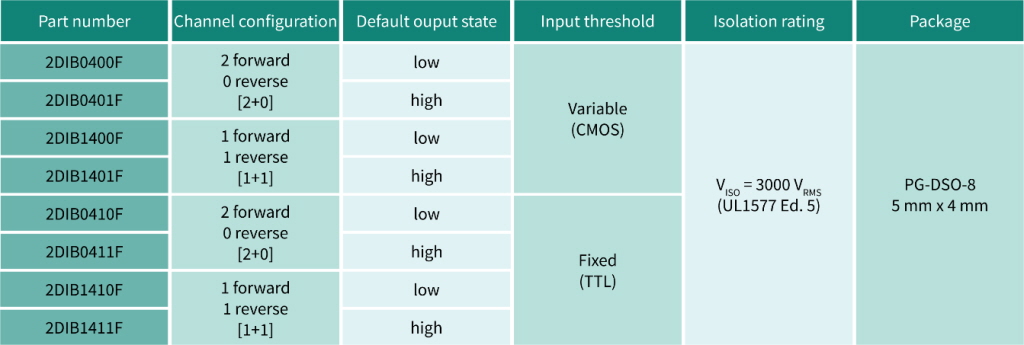
▲표 2 : ISOFACE™ 듀얼 채널 디지털 아이솔레이터 2DIBx4xxF 제품군의 제품 구성
이 듀얼 채널 디지털 아이솔레이터 제품군은 부품 차원에서 UL-1577 및 IEC 60747-17(VDE 0884-17) 표준에 대한 인증과 텔레콤 및 서버 애플리케이션 용으로 IEC 62368-1 같은 시스템 차원 인증을 취득하고 있다. 또한 4mm의 연면거리 및 공간거리는 저전압 DC-DC 브릭, 상측 플로팅 드라이브, 절연형 UART/CAN 통신 같이 기본 절연을 필요로 하는 애플리케이션에 사용하기에 잘 맞는다.
표 3은 인피니언의 ISOFACE™ 듀얼 채널 디지털 아이솔레이터의 제품 특징과 이점을 요약해서 보여준다.
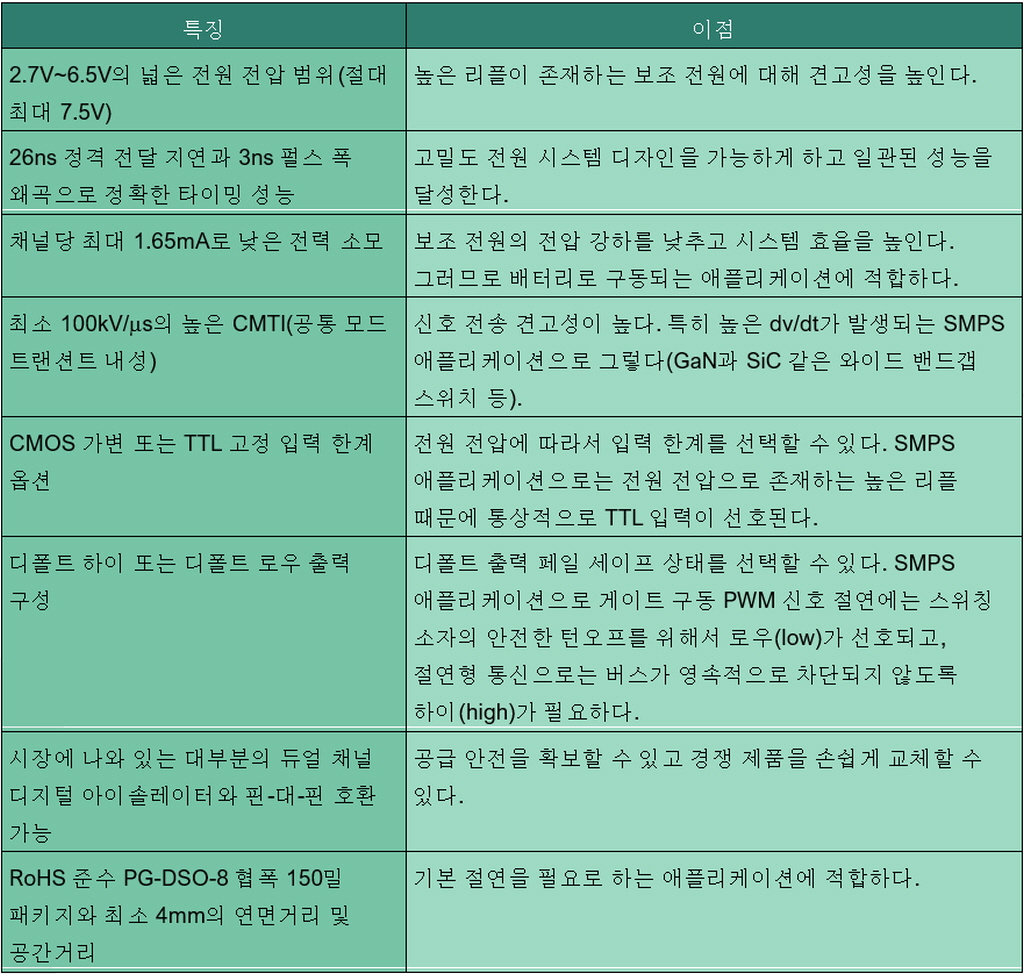
▲표 3 : ISOFACE™ 듀얼 채널 디지털 아이솔레이터의 제품 특징과 이점
■ ISOFACE™ 듀얼 채널 디지털 아이솔레이터의 애플리케이션 예
○ 절연형 저전압 DC-DC 브릭
텔레콤 및 서버의 스위치드 모드 전원장치(SMPS)로 안정적인 12VDC 출력을 달성하기 위해서 저전압 DC-DC 브릭이 널리 사용된다[4].
전력 밀도, 안전, 통신 용량에 대한 갈수록 높아지는 요구를 충족하기 위해서 800W 이상의 절연형 DC-DC 브릭에는 풀브리지 대 풀브리지(FB-FB) 토폴로지를 주로 사용한다.
제어를 담당하는 것은 메인 전원 트랜스포머의 이차 측에 있는 디지털 컨트롤러이다. 입력-대-출력 안전 절연으로 절연 배리어를 통해서 PWM 게이트 제어 신호를 전달하기 위해서 기본 절연 성능의 디지털 아이솔레이터를 흔히 사용한다.
그림 3은 절연형 1kW DC-DC 브릭 용으로 인피니언의 솔루션을 보여준다. 일차 측 풀브리지 토폴로지를 제어하기 위해서 이차 측의 XDP™ XDPP1100 디지털 전원 컨트롤러를 사용한다.
ISOFACE™ 듀얼 채널 디지털 아이솔레이터 2DIB0410F가 절연 배리어를 통해서 PWM 신호를 전달한다.
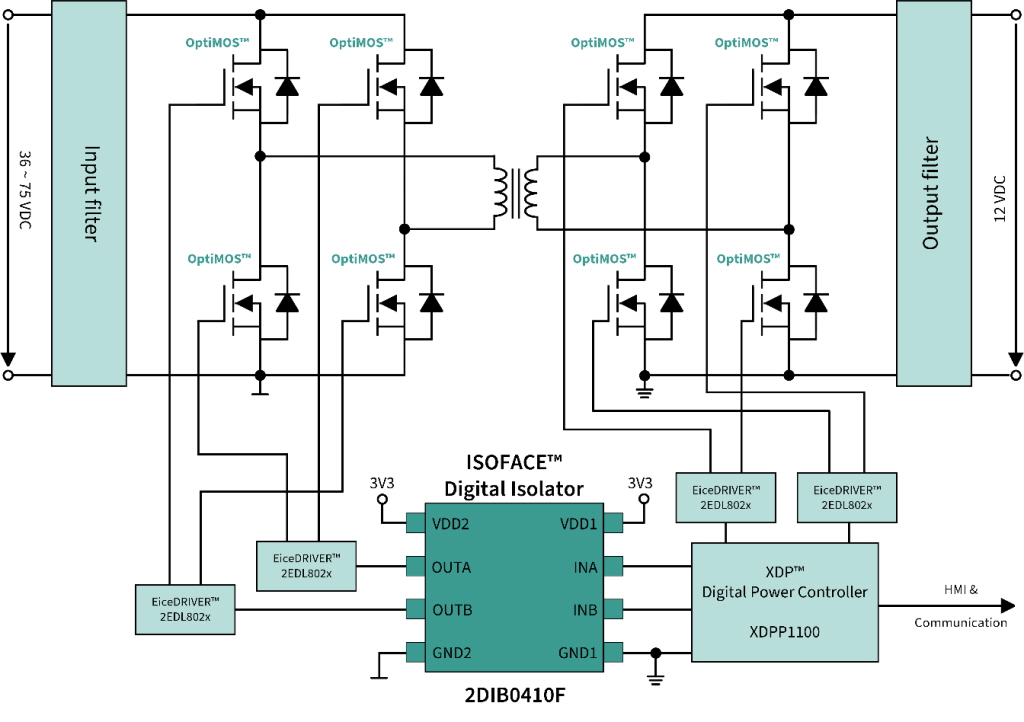
▲그림 3 : ISOFACE™ 2DIB0410F를 채택한 절연형 저전압 DC-DC 블릭
이 컨버터의 양쪽으로 레벨 쉬프트 EiceDRIVER™ 2EDL802x 게이트 드라이버 IC를 사용한다.
디지털 아이솔레이터의 2개 채널이 상보형 PWM 신호를 전달해서 풀브리지의 양쪽 암으로 대각선으로 2개 OptiMOS™ 전력 MOSFET을 제어한다.
또한 ISOFACE™ 2DIB0410F가 고정적 TTL 입력 한계를 제공한다. 그러므로 SMPS 애플리케이션으로 VDD 전원 라인 잡음에 대한 내성을 높인다.
디폴트 로우 출력 상태는 디지털 아이솔레이터의 입력 측 전원이 UVLO보다 낮을 때 모든 MOSFET을 안전하게 턴오프시킨다.
○ 절연형 CAN 및 UART 통신
CAN(Controller Area Network) 및 UART(Universal Asynchronous Receiver/Transmitter) 통신은 산업용 및 자동차 애플리케이션에 널리 사용되고 있다.
데이터 전송을 위해서 물리 층으로 한 쌍의 케이블(2개 통신 라인)만을 필요로 한다는 점이 공통적인 장점이다.
절연형 CAN 또는 UART 인터페이스로 안전을 확보하고 잡음 간섭을 방지하기 위해서는 ISOFACE™ 듀얼 채널 디지털 아이솔레이터 2DIB1401F가 갈바닉 절연을 위한 뛰어난 솔루션을 제공한다.
이 신뢰할 수 있는 아이솔레이터는 높은 CMTI와 극히 낮은 펄스 폭 왜곡(PWD)을 특징으로 한다. 이러한 특징들은 신뢰할 수 있는 통신을 달성하기 위해서 중요하다.
또한 이 아이솔레이터는 디폴트 하이 출력 상태로 결함이 발생되더라도 통신 라인(통상적으로 휴지 상태일 때 로직 하이)이 차단되지 않도록 함으로써, 입력 측으로 혹시 발생될 수 있는 전원 소실을 방지한다.
그림 4는 인피니언의 CAN 트랜시버 TLE9251을 함께 사용한 절연형 CAN 인터페이스 예를 보여준다.
ISOFACE™ 2DIB1401F가 컨트롤러와 트랜시버 사이에서 갈바닉 절연을 제공한다.
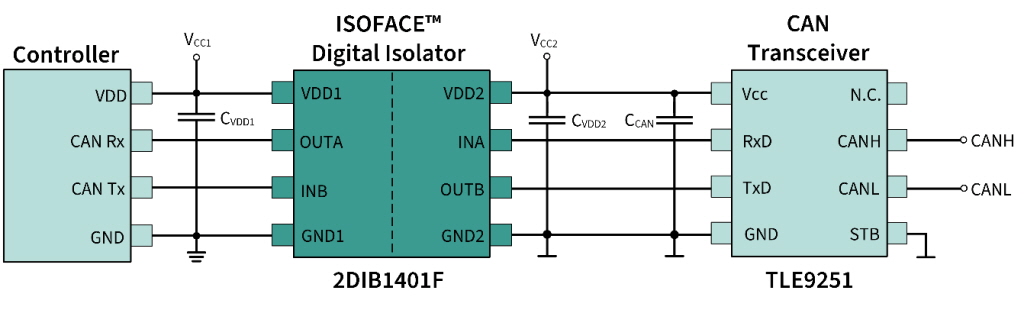
▲그림 4 : ISOFACE™ 2DIB1401F를 채택한 절연형 CAN(Controller Area Network) 통신
○ GaN IPS 하프 브리지의 기능적 절연
최근 들어서 SMPS 디자인으로 650V 갈륨 나이트라이드(GaN) HEMT가 갈수록 중요해지고 있다. 이것은 이 HEMT가 훨씬 더 높은 스위칭 주파수로 동작할 수 있고 에너지 손실을 최소화하기 때문이다. 단일 패키지로 GaN 스위치와 게이트 드라이버를 통합한 GaN IPS(Integrated Power Stage) 또한 극히 높은 전력 밀도를 달성하고, 부품 수를 줄이고, 기생성분을 최소화할 수 있다는 점에서 인기가 높아지고 있다.
상측 GaN IPS가 적절히 작동하기 위해서 게이트 드라이버로 레벨 쉬프트 기능을 위해서 디지털 아이솔레이터가 필요하다. 게이트 드라이버가 스위칭 노드를 참조하기 때문이다. GaN HEMT는 100V/ns에 이르는 빠른 dv/dt 통신을 발생시키기 때문에 높은 공통 모드 트랜지언트가 발생될 수 있다. 그러므로 견고한 솔루션을 필요로 한다. 이럴 때 ISOFACE™ 디지털 아이솔레이터가 최소 100V/ns의 CMTI로 PWM 신호를 신뢰하게 전달한다.
그림 5는 상측 플로팅 드라이브로 ISOFACE™ 듀얼 채널 디지털 아이솔레이터 2DIB1410F를 사용한 예를 보여준다. 순방향 데이터 채널은 게이트 신호를 전달하고, 역 채널은 컨트롤러로 결함 피드백 신호를 통신한다.
선택적으로 하측 GaN IPS로 또 다른 ISOFACE™ 2DIB1410F를 사용할 수 있다. 상측과 하측 신호 경로 사이에 전달 지연을 같게 하고 GaN IPS(전원 접지)와 컨트롤러(디지털 접지)의 서로 다른 접지로 절연을 제공하기 위해서 이렇게 하는 것을 강력하게 권장한다.
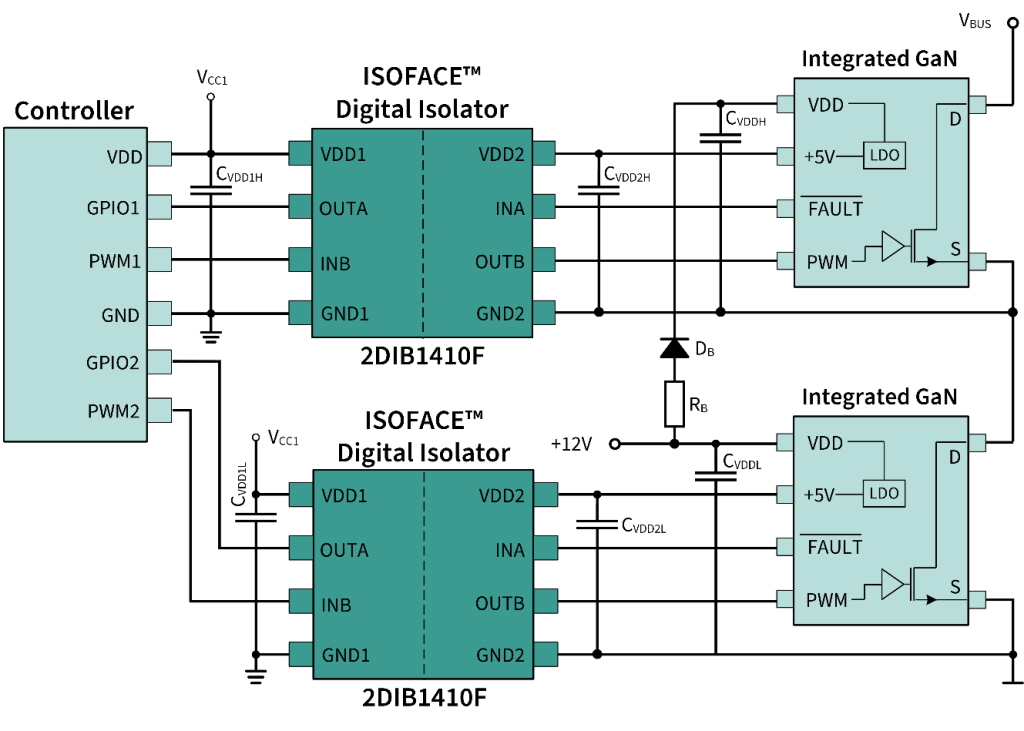
▲그림 5 : GaN IPS 하프 브리지로 ISOFACE™ 2DIB1410F를 사용한 기능적 절연
■ 맺음말
인피니언의 앞선 ISOFACE™ 디지털 아이솔레이터는 낮은 전류 소모, 향상된 공통 모드 트랜지언트 내성, 높은 전달 지연 정확도를 특징으로 함으로써, 고전압 디지털 제어 애플리케이션에 사용하도록 견고하고도 신뢰할 수 있는 솔루션을 제공한다.
여기에다 XDP™ 디지털 컨트롤러, EiceDRIVER™ 게이트 드라이버 IC, 전력 스위치(OptiMOS™, CoolMOS™, CoolSiC™, CoolGaN™) 같은 Infineon의 여타 제품들을 결합함으로써 최신 전력 전자 애플리케이션으로 갈수록 높아지는 절연 요구를 충족하는 전체적인 시스템 솔루션을 달성할 수 있다.
Infineon의 앞선 기술을 활용해서 고객들이 고전압 디지털 제어 애플리케이션으로 갈수록 높아지는 절연 요구를 충족하고 더 우수한 시스템 성능과 더 높은 신뢰성을 달성할 수 있을 것이다.
여기를 클릭하면 인피니언의 ISOFACE™ 디지털 아이솔레이터에 관한 더 자세한 정보를 볼 수 있다.
※ 저자
Jiaxin Tian, Senior Staff Product Application Engineer,
Dr. Narayanaswamy Swaminathan, Staff Product Definition Engineer,
Dr. Diogo Varajao, Head of Technical Marketing of Isolation ICs,
※ 참고문헌
[1] D. Varajao, C. Menditti Matrisciano, "Isolated gate driving solutions - Increasing power density and robustness with isolated gate driver ICs," Infineon Technologies AG, Application Note v1.1, AN_1909_PL52_1010_201256, June 2022
[2] C. Menditti Matrisciano, T. Beer, D. Varajao, Infineon Technologies AG, "Using the EiceDRIVER™ 2EDi product family of dual-channel functional and reinforced isolated MOSFET gate drivers," Infineon Technologies AG, AN_1805_PL52_1806_095202, 2019
[3] W. Frank, H. Rettinger, "New International Standard for Magnetic and Capacitive Couplers," Bodo's Power Systems, November 2020, p. 40-43
[4] D. Varajao, C. Menditti Matrisciano, "Dual-channel isolated EiceDRIVER™ 2EDF7275K in telecom bricks - Application example in a 600 W quarter-brick 48 V to 12 V full-bridge to full-bridge rectifier evaluation board," Infineon Technologies AG, AN_2002_PL52_2003_165036, 2020