지난 20일 머크(Merck)는 기자간담회를 통해 ‘머티리얼즈 인텔리전스 플랫폼 기반 기술 혁신’을 발표했다. 발표를 담당한 아난드 남비아(Anand Nambiar) 머크(Merck) 일렉트로닉스 비즈니스 수석부사장 겸 CCO는 AI 시뮬레이션을 통해 수백, 수천건의 아이디어를 찾아낼 수도 있으며, 가상 실험을 통해 제품의 개선 시간을 크게 단축할 수 있다고 밝혔다. 이를 통해 고객사와 협업해 반도체 모든 단계를 지원하고 있다고 전했다. 이에 본지는 아난드 남비아 머크 수석부사장과 인터뷰를 통해 한국의 투자와 고객 협업 사례를 들어봤다.
“‘머티리얼즈 인텔리전스’, 반도체 혁신 빠르게 달성”
반도체 전공정 지원하는 머크, 고객사들 빠른 문제 해결 기대 높아
AI로 반도체 소재 수천번 시뮬레이션, 개선점 찾아 소재 혁신 기여
[편집자주] 지난 20일 머크(Merck)는 기자간담회를 통해 ‘머티리얼즈 인텔리전스 플랫폼 기반 기술 혁신’을 발표했다. 발표를 담당한 아난드 남비아(Anand Nambiar) 머크(Merck) 일렉트로닉스 비즈니스 수석부사장 겸 CCO는 AI 시뮬레이션을 통해 수백, 수천건의 아이디어를 찾아낼 수도 있으며, 가상 실험을 통해 제품의 개선 시간을 크게 단축할 수 있다고 밝혔다. 이를 통해 고객사와 협업해 반도체 모든 단계를 지원하고 있다고 전했다. 이에 본지는 아난드 남비아 머크 수석부사장과 인터뷰를 통해 한국의 투자와 고객 협업 사례를 들어봤다.
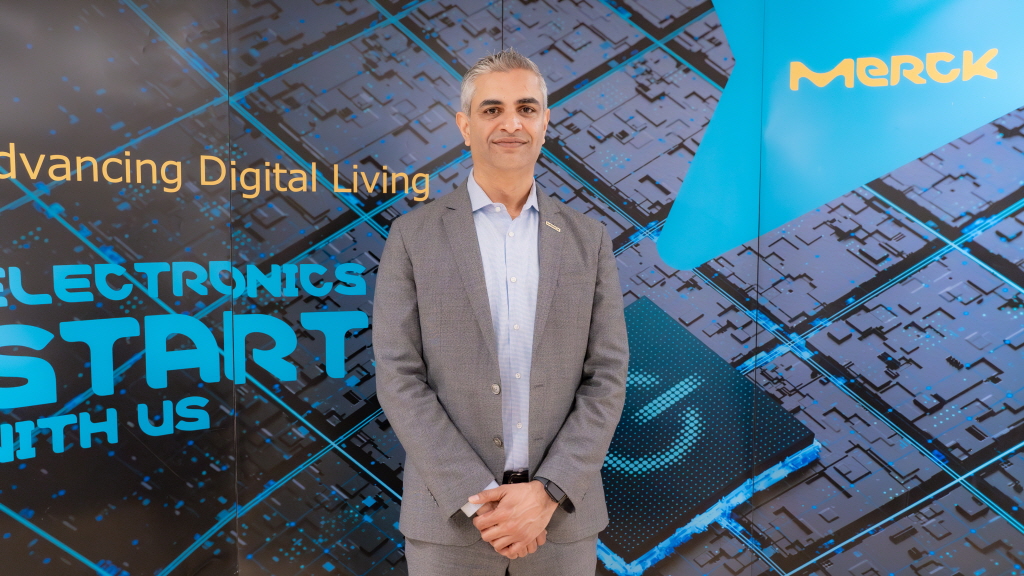
▲아난드 남비아(Anand Nambiar) 머크(Merck) 일렉트로닉스 비즈니스 수석부사장 겸 CCO
■ 한국 투자에 대한 상황을 알고 싶다
머크는 2년 전에 레벨업 프로그램을 발표한 바 있고, 그중에서 한국에 대해서는 6억 유로에 대한 투자를 기획한 바가 있다.
지금까지 그 금액에 대한 상당한 금액이 집행이 된 상황이고, 앞으로 더 필요한 부분에 대해서 적절한 투자와 집행을 해 나갈 예정이다.
한국에서는 12개의 사업장을 유지하고 있고, 1,700여명의 임직원이 근무하고 있다.
머크의 생산량 확대는 유기적인 인수를 통해 성장하고 있다.
■ 삼성전자나 SK하이닉스 등 국내 반도체 기업들과 어떻게 협업하고 있는지 궁금하다.
머크는 반도체 소재 업계에 있어 매우 독특한 기업이라고 할 수 있다.
그 이유는 반도체 공정에 있어서 필요한 △리소그래피 △증착 △CMP △에칭 △패키징 등 모든 단계를 총망라해 각각의 영역에 필요한 제품들과 프로세스를 제공하고 있는 회사이기 때문이다.
따라서 반도체 제조 생산과 관련된 삼성전자 및 SK하이닉스 등이 필요로 하는 모든 영역에 대한 플랫폼을 제공하고 있고, 가장 광범위한 포트폴리오를 갖추고 있다.
이에 고객사들은 보다 나은 조합의 솔루션을 제공하기를 우리에게 기대하고 있다.
우리는 고객사들의 제품 생산에서 출시까지의 시간을 단축하고, R&D, 생산성 등을 빠르게 높여나가는 것을 지원하고 있다.
따라서 우리가 이런 고객사들과 협업을 한 분야들은 EUV, 리소그래피, 새로운 형태의 금속들, 에칭용 특수가스, Low GWP 관련 부분들이다.
또한 그 외에도 반도체용 과불화화합물(PFAS)이 들어있지 않은 리소그래피 관련 포트폴리오를 개발해서 제공하려고 노력하고 있다.
삼성전자와 SK하이닉스는 양사 모두 메모리, 그리고 삼성전자 같은 경우는 파운드리 분야까지 세계적으로 기술을 이끄는 선도기업 중 하나이기 때문에 리더 기업들이 직업하고 있는 복잡한 문제들을 해결하기 위해서 다방면으로 협업하고 있다.
■ 한국에서 반도체 산업 지원책으로 주 52시간 예외에 대해 많이 논의되고 있다. 주 52시간 예외 적용이 반도체 경쟁력 강화에 도움이 될 것으로 보는지
제가 답변드리기에는 어려운 질문이다.
업계에서는 훨씬 더 빠르고 신속하게 혁신이 필요한 것은 자명하나 이것이 단순하게 업무의 시간이 늘어나는 것으로만 해결이 되는 것이 아니다.
혁신을 추구하는 방식을 스마트하게 바꾸면서 달성할 수 있다고 생각한다.
머크에서는 머티리얼즈 인텔리전스라는 것을 도입하고 있다.
과거에는 어떠한 실험을 통해서 고칠 것을 확인하고, 또 실험을 통해서 결과를 확인하는 과정을 반복했다고 한다면 요즘은 AI와 AI 시뮬레이션 툴을 이용한다.
이를 통해 개발의 어떤 디자인 단계에서부터 수만 수천가지 경우의 수를 시뮬레이션해 본 다음에 그중에서 적절한 것들을 골라서 실험 단계로 넘어간다.
그런 시대를 살고 있기 때문에 시간의 추가적인 투입도 중요하지만 그것뿐만 아니라 생태계 내에서 어떻게 협업하고, 혁신을 추구하고 있는지에 대한 방식에서 스마트화가 필요하다고 생각된다.
또한 이것이 서플라이체인 내에서 협업이 이뤄져야 한다고 생각된다.