[편집자주] 제조 산업에서 엔지니어링 소프트웨어는 현 시대에 한 몸이나 다름없다. 시뮬레이션 기반 설계로 프로세스의 효율성을 도모하는 한편 AI 기반 설계까지 등장하며 중요한 기술 도약의 분기점을 맞이하고 있다. 최근 하드웨어 스펙이 점차 증가하며 전자파 환경 노이즈 또한 동시에 증가하고 있는 가운데 엔지니어링 툴은 EMI/EMC 대응책을 지속 개발하며 발전해 나가고 있다. 이번 ‘EMI/EMC 명사(名士) 대담’에서는 EMI·EMC 분야 엔지니어링 소프트웨어 솔루션 전문가를 만나 이야기를 나눴다.
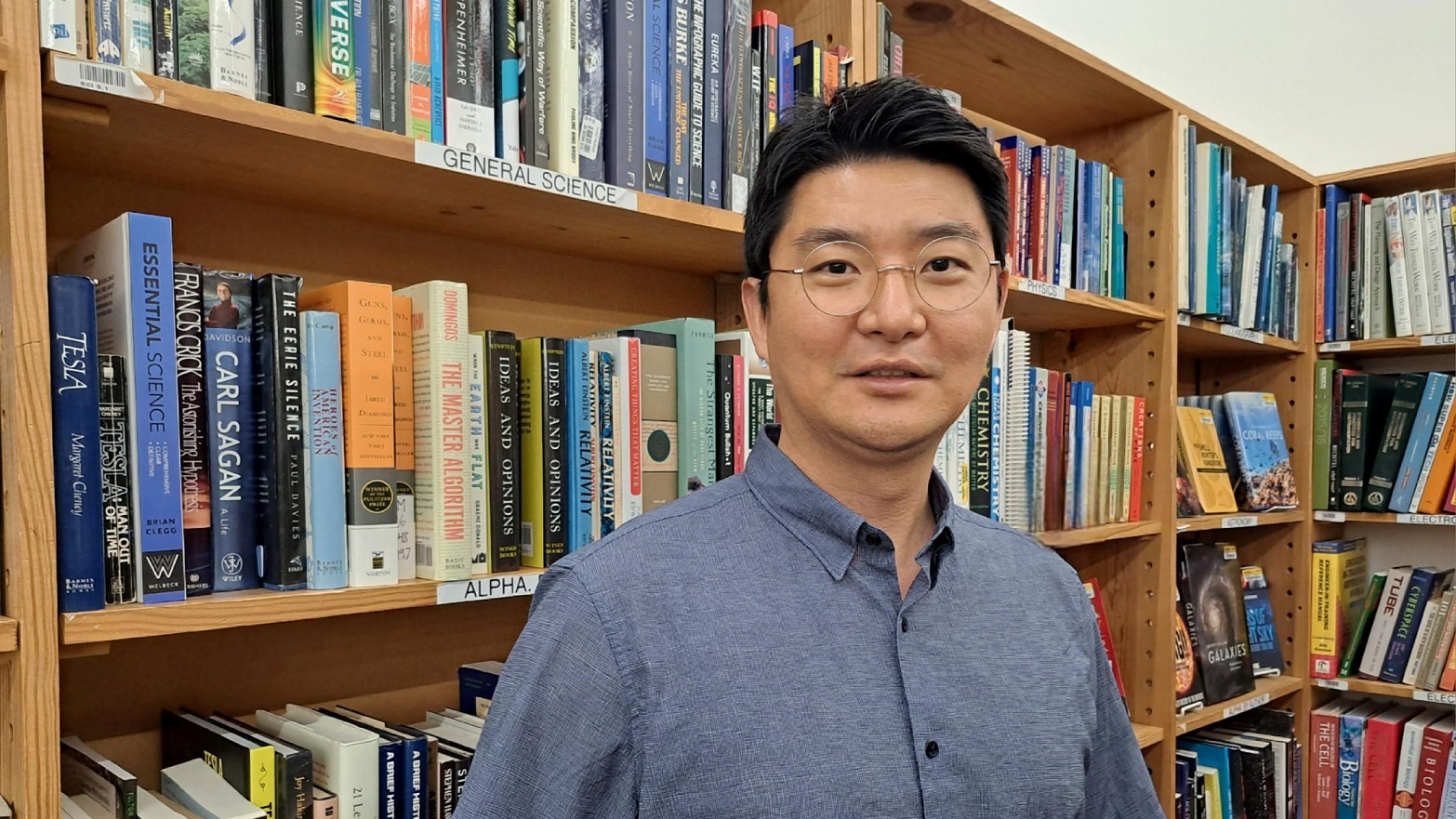
▲알테어 이준상 박사
EMC SW 엔지니어, 분석도구 비전 설정·전략 개발
SBD 필요성, 비용 효율·시간절약·성능 향상·정밀성
AI 기반 가상 시뮬레이션, EMC 시험 필요성↓ 전망
[편집자주] 제조 산업에서 엔지니어링 소프트웨어는 현 시대에 한 몸이나 다름없다. 시뮬레이션 기반 설계로 프로세스의 효율성을 도모하는 한편 AI 기반 설계까지 등장하며 중요한 기술 도약의 분기점을 맞이하고 있다. 최근 하드웨어 스펙이 점차 증가하며 전자파 환경 노이즈 또한 동시에 증가하고 있는 가운데 엔지니어링 툴은 EMI/EMC 대응책을 지속 개발하며 발전해 나가고 있다. 이번 ‘EMI/EMC 명사(名士) 대담’에서는 EMI·EMC 분야 엔지니어링 소프트웨어 솔루션 전문가를 만나 이야기를 나눴다.
알테어엔지니어링에서 근무하는 이준상 박사와의 EMI/EMC 명사(名士) 대담을 통해 활동 근황과 EMI/EMC 설계·시뮬레이션 도구 및 발전 추세를 들을 수 있었다.
[기자] 안녕하세요 간단한 자기소개 부탁드립니다.
[이준상 박사] 저는 성균관대학교 나완수 교수님 연구실에서 자동차 EMC를 주제로 박사 학위를 받았으며, 2012년부터 자동차 EMC 분야에서 경력을 쌓아 왔습니다.
현재는 미국 텍사스 주 오스틴에서 알테어엔지니어링(Altair Engineering)의 프로덕트 매니저로 근무하고 있습니다. 주된 업무는 EMC 솔루션을 기획하고 소프트웨어 개발자와 협력해 분석 도구를 만드는 것입니다.
자동차 부품, 특히 PCB 시스템이 포함된 부품의 EMC 엔지니어링에 대한 다양한 경험을 가지고 3년 전 알테어에 입사를 했습니다. EMC를 전공한 후 해당 분야에서 경력을 쌓은 엔지니어로써 소프트웨어 회사에서 할 수 있는 역할은 EMC 분석 도구의 비전을 설정하고 전략을 개발하며, 시장 조사와 사용자 연구를 통해 제품의 발전 방향을 결정하는 것입니다.
이러한 과정을 통해 제품 로드맵을 작성하고, 우선순위를 정해 제품이 사용자와 시장의 요구에 부합하도록 관리하고 있습니다.
[기자] 회사 및 학회 등에서 활동이 왕성하실 텐데 최근 활동들에 대해서 소개해주세요.
[이준상 박사] 최근 미국에서는 자동차와 중공업 분야에서 EMC 솔루션을 요구가 증가하고 있습니다. 한국에는 잘 알려지지 않은 에머슨(Emerson)과 존 디어(John Deere)와 같은 회사와 EMC 관련 기술논의를 하고 있습니다.
물론 GM과 포드(Ford)도 최신 트랜드에 맞는 업데이트된 EMC 솔루션을 지속적으로 요구하고 있습니다.
학술 활동의 경우 IEEE EMC+SIPI symposium과 DesignCon에 참석하고 있습니다. 올해2024년도 미국 애리조나 피닉스에서 개최되는 2024 IEEE EMC+SIPI symposium에 참석해‘Automated SI Verification Methods for Optimal Design of DDR Systems’를 발표할 예정입니다.
지난해는 DesignCon에 참석해 ‘An EMI Reduction Modeling Approach of PCB & Shielding Enclosures Using the Lua-based Automation’, 2022년엔 IEEE EMC+SIPI에서 ‘High-speed Memory Signal Integrity Compliance using the CNN’을 발표한 바 있습니다.
[기자] 전력전자 분야에서 최근 화두가 되고 있는 EMI/EMC 이슈는 무엇이 있나요? 관심 있게 보신 아젠다가 있으면 말씀 부탁드립니다.
[이준상 박사] 전력전자 EMC 엔지니어의 주요 요구 사항은 원격 접지(Remote ground)와 로컬 접지(Local ground)를 시뮬레이션하는 것입니다.
이 접지 연결은 Component-level EMC를 측정할 때 필요한 테스트 조건입니다(예: CISPR25). 로컬 접지는 제품 외함과 EMC 테스트 시 사용되는 접지 테이블을 접지하는 방법이며, 원격 접지는 접지를 하지 않는 방법입니다. 제품이 시스템에 설치될 때 시스템 접지(예: 차량 차체)에 접지될 수도 있고 그렇지 않을 수도 있습니다.
각 경우에서 공통 모드 노이즈의 경로가 다르기 때문에 EMI 결과도 큰 차이를 보입니다. 전력 전자 EMC 엔지니어는 두 가지 경우를 모두 시뮬레이션하고자 하며, 시뮬레이션 업계에 있는 알테어와 같은 회사는 정확한 결과와 빠른 실행 시간을 제공하기 위해 수치 해석(Numerical analysis) 방법을 최적화하는 연구를 진행하고 있습니다.
[기자] 알테어에 근무한 지는 얼마나 됐나요?
[이준상 박사] 저는 알테어 코리아에서 3년간 근무했습니다. 최근에는 미국의 알테어 본사로 이전했습니다.
[기자] 알테어는 어떤 기업인가요?
[이준상 박사] 알테어는 엔지니어링 시뮬레이션, 데이터 분석, 그리고 고성능 컴퓨팅(HPC) 분야에서 선도적인 소프트웨어 및 클라우드 솔루션을 제공하는 글로벌 기업입니다. 제품 설계, 최적화, 그리고 성능 향상을 지원해 엔지니어들이 혁신적인 제품을 보다 빠르고 효율적으로 개발할 수 있도록 돕습니다.
예를 들어, 자동차 CAE 엔지니어는 알테어의 도구를 사용해 차량 공기역학(유체 시뮬레이션)을 최적화하고, 구조적 무결성(기계 시뮬레이션)을 개선하며, 고급 전자 시스템(전자 시뮬레이션)을 설계할 수 있습니다.
또한, 알테어의 AI 기반 솔루션은 제품의 성능을 예측하고 오랜 기간동안 유지보수가 될 수 있도록 성능 최적화를 가능하게 합니다.
알테어 코리아는 이러한 기술을 한국 시장에 맞추어 제공하고 있으며, 다양한 산업 분야에서 고객들의 엔지니어링 문제를 해결하는 데 중점을 두고 있습니다. 특히 자동차, 항공, 전자 등 다양한 분야에서 알테어의 시뮬레이션 및 데이터 분석 도구를 제공하고 있습니다.
[기자] 시뮬레이션 기반 설계가 중요한 이유는 무엇입니까?
[이준상 박사] 시뮬레이션 기반 설계(Simulation-Based Design, SBD)는 공학 및 제조 산업에 혁신적인 영향을 미치며, 그 중요성은 여러 가지 측면에서 두드러지고 있습니다.
첫째, 비용 효율성 측면에서 SBD는 물리적 프로토타입 제조의 필요성을 크게 줄입니다. 엔지니어는 가상으로 제품을 테스트하고 반복할 수 있어, 비용이 많이 드는 물리적 프로토타입을 줄일 수 있습니다. 또한, 개발 과정 초기부터 잠재적인 설계 결함과 성능 문제를 식별하고 해결할 수 있어, 사후 수정 작업에 드는 비용을 절감할 수 있습니다.
둘째, SBD는 시간 절약 측면에서도 큰 장점을 제공합니다. 가상 테스트는 설계 과정을 가속화하여 더 빠른 반복과 시장 출시 시간을 단축시킵니다. 동시 공학을 통해 설계의 여러 측면을 동시에 평가할 수 있어 전체 효율성을 높일 수 있습니다. 이로 인해 제품 개발 주기가 단축되고, 더 신속하게 시장에 제품을 출시할 수 있습니다.
셋째, SBD는 제품 성능을 향상시키는 데 중요한 역할을 합니다. 엔지니어는 시뮬레이션을 통해 다양한 매개변수를 최적화함으로써 더 나은 성능을 가진 제품을 설계할 수 있습니다. 또한, SBD는 물리적으로 테스트하기에 너무 위험하거나 비용이 많이 드는 혁신적인 설계를 실험할 수 있는 기회를 제공합니다.
넷째, SBD는 정확성과 정밀성을 향상시키는 데 기여합니다. 현대 시뮬레이션 도구는 복잡한 물리적 현상을 높은 정확도로 모델링하여, 실제 성능에 대한 신뢰할 수 있는 통찰을 제공합니다. 다양한 시나리오, 특히 극한 조건을 포함한 상황을 평가할 수 있어 제품의 강도와 내구성을 보장할 수 있습니다.
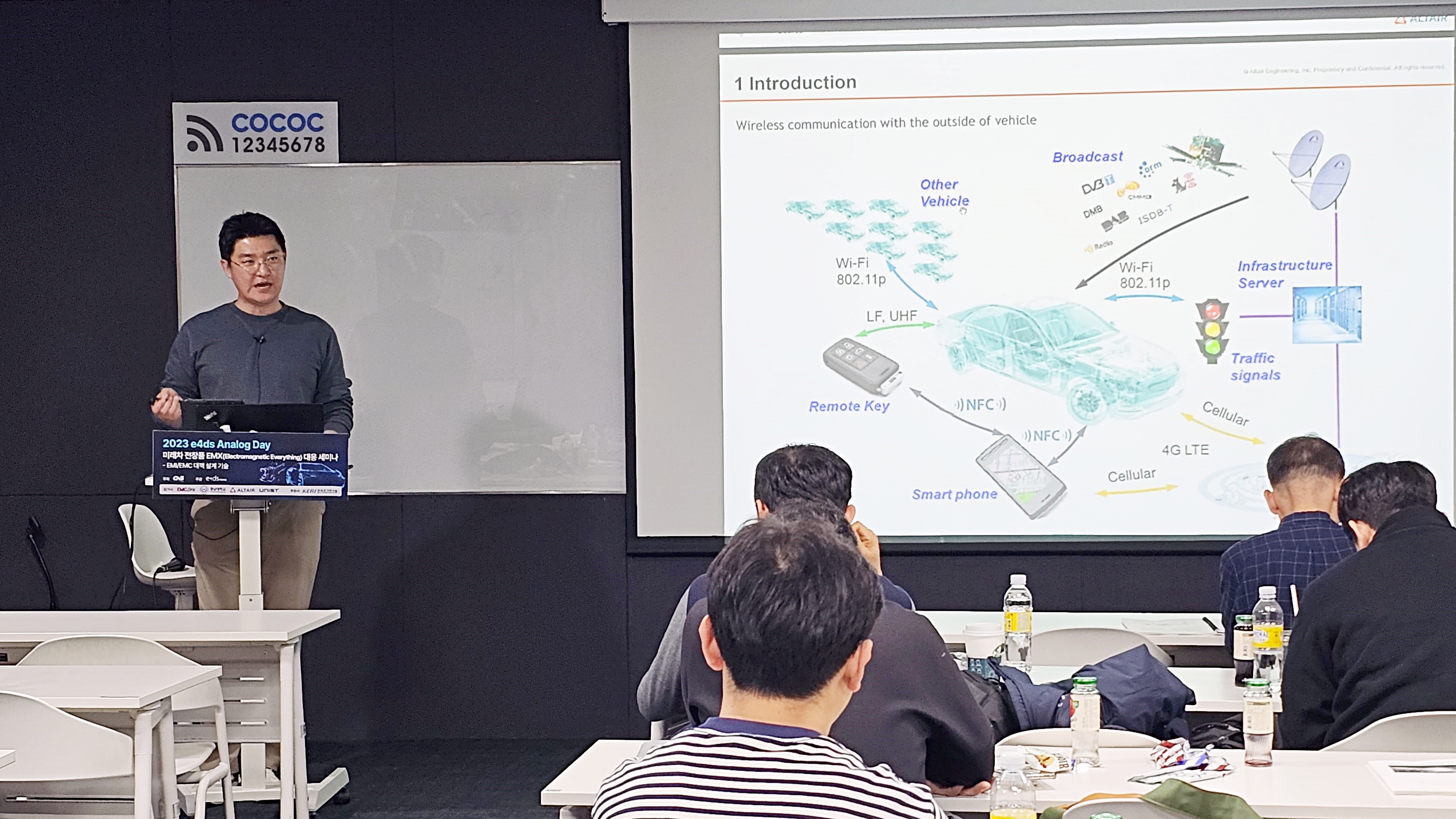
▲e4ds 아날로그 데이 2023에서 이준상 박사가 강연하고 있다.
[기자] 알테어가 보유한 EMI/EMC 관련 툴에 대해 소개 부탁드립니다.
[이준상 박사] 알테어는 1985년 설립이래로 기계적(Mechanical) 시뮬레이션에 정평이 나있는 회사였습니다. 전자적(Electrical) 시뮬레이션 능력을 강화하기 위해 최근 몇년간 전략적으로 PSIM, Feko, PollEx를 인수해 전자 분야 시뮬레이션에서 부족했던 부분을 채워가며 상당한 발전을 이루었습니다.
이 중 PSIM은 전력 전자 회로의 전도성 방출 시뮬레이션에 탁월한 도구로 알려져 있습니다. 이 도구는 엔지니어가 전력 전자 장치의 동작을 모델링하고 전도성 방출을 예측할 수 있게 해 EMC 규정을 준수하는 데 매우 중요합니다.
반면, Feko는 방사성 방출 시뮬레이션에 강력한 도구입니다. 이 도구는 전자기파의 전파 및 파동 입장에서 다양한 구조 간의 상호작용을 분석할 수 있게 해줍니다. 이는 방사성 방출이 제품 성능과 EMC 규제 표준 준수에 영향을 미칠 수 있는 모바일 및 소비자 전자 제품 시뮬레이션에 활용 되고 있습니다.
PollEx는 안정적인 ECAD 가져오기 기능과 IBIS 모델을 사용하여 회로의 전류 소스를 모델링하는 기능을 제공합니다. PollEx는 신호 무결성과 전력 무결성 시뮬레이션의 정확성을 보장해 복잡한 PCB 시스템의 전기적 신뢰도를 향상 할 수 있습니다.
[기자] 툴들이 굉장히 세분화돼 있습니다. 통합 환경에서 활용할 수도 있나요?
[이준상 박사] 기존에는 이들 도구는 각각 독립적으로 사용돼 엔지니어들이 시간 소모적인 시뮬레이션을 개별적으로 수행해야 했습니다. 그러나 알테어는 이러한 솔버를 SimLab이라는 플랫폼에 통합해 사용자 편의성과 시뮬레이션 효율성을 크게 향상시키는 작업을 하고 있습니다. 이 통합은 전기적 특성뿐만 아니라 열 및 기계적 상호작용을 고려한 포괄적인 다중 물리 시뮬레이션을 가능하게 할 것입니다.
[기자] 시중에 비슷한 유형의 툴들이 많습니다. 경쟁사 대비 알테어의 툴의 특장점은 무엇인가요?
[이준상 박사] 알테어의 PSIM 툴은 전력전자 설계와 시뮬레이션 분야에서 여러 경쟁사 제품에 비해 몇가지 장점과 특성을 지니고 있습니다.
PSIM은 주로 전력전자 시스템의 설계, 최적화, 검증을 목적으로 사용됩니다. 알테어의 PSIM은 직관적인 사용자 인터페이스 및 예제를 제공해 사용자들이 쉽게 모델을 구축하고 시뮬레이션을 수행할 수 있도록 돕습니다. 이는 설계 초보자뿐만 아니라 숙련된 엔지니어들에게도 큰 장점으로 작용합니다.
또한 매크로 타입의 PSIM 고유의 Spice 라이브러리는 복잡한 회로와 시스템을 신속하게 분석할 수 있습니다. 그리고 다양한 전력전자 부품과 시스템 모델을 포함하는 방대한 라이브러리를 제공합니다. 이를 통해 사용자들은 다양한 시나리오를 쉽게 설정하고 테스트할 수 있습니다.
[기자] 현재 회로설계와 EMI/EMC 영역에서 AI 기반 설계는 어떤 방식으로 활용되고 있나요?
[이준상 박사] 저희 회사 기준으로 이야기를 드리면 알테어는 최근 RapidMiner라는 회사를 인수해 코드 없는 AI 소프트웨어를 제공하고 있습니다. 스크립트를 직접 코딩하지 않고도 시뮬레이션 데이터를 분석하고 최적화된 설계 매개변수를 제공합니다. 이는 공학 시뮬레이션에서 가장 많이 활용하고 있는 설계 최적화 과정을 단순화 합니다.
앞으로 AI 기반 설계는 EMI/EMC 분야에서 중요한 변화를 가져올 것으로 기대됩니다. AI는 구성 요소 간 복잡한 상호작용과 전자기장을 보다 포괄적으로 모델링해 예측 정확도를 향상시킬 것으로 예상됩니다. 이는 더 나은 가상 시뮬레이션을 통해 실제 EMC 시험의 필요성을 줄일 수 있는 스마트한 EMC 설계 전략을 가능하게 할 것입니다.
또한, AI 기반 시뮬레이션 도구들은 BOM에서 부품(예를 들어capacitor와 같은 수동소자)이 변경되면 실시간 EMI/EMC 성능을 모니터링하고 부품 최적화 전략 제공을 가능하게 함으로써 EMI/EMC 규정 준수와 신뢰성을 agile하게 보장할 수 있을 것입니다. 전반적으로 AI는 EMI/EMC 규정 준수 과정을 간소화하고 설계 주기를 가속화하며 전자 제조 산업에서 혁신을 촉진할 것입니다.
[기자] 앞으로의 계획과 목표가 있으시다면 한 말씀 부탁드립니다.
[이준상 박사] 앞으로 저는 알테어의 글로벌R&D 네트워크를 활용해 EMC 관련 협업을 강화할 계획입니다. 특히, 미국에 기반을 두고있는 자동차 및 중공업 분야의 주요 고객들과 긴밀히 협력해 EMC 시뮬레이션 기술을 더욱 발전시키고, 이를 활용해 유럽과 아시아지역의 EMC 요구사항에 맞춘 맞춤형 솔루션을 제공할 것입니다. 이를 통해 알테어의 글로벌 시장에서의 입지를 더욱 확고히 하고, 다양한 영역에서 시뮬레이션 혁신을 주도하고 싶습니다.
감사합니다.