과학기술정보통신부 산하 정부출연연구기관인 한국재료연구원(KIMS, 원장 최철진)이 상용 가능 수준의 원스텝 전극 제공 공정 기술을 국내 최초로 개발하며, 음이온교환막 수전해 국산화에 성큼 다가섰다.
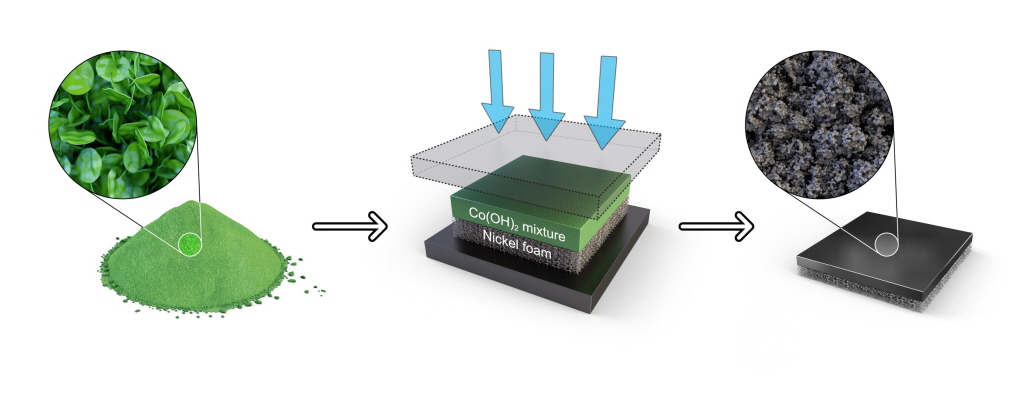
▲one-step 산소발생 전극 제조 공정 모식도
재료硏, 상용 가능 수준의 원스텝 전극 제조 공정 기술 국내 최초 개발
과학기술정보통신부 산하 정부출연연구기관인 한국재료연구원(KIMS, 원장 최철진)이 상용 가능 수준의 원스텝 전극 제공 공정 기술을 국내 최초로 개발하며, 음이온교환막 수전해 국산화에 성큼 다가섰다.
재료연은 최승목 박사 연구팀이 음이온교환막 수전해의 핵심 부품인 전극을 원료물질로부터 바로 양산 가능 수준으로 만드는 원스텝 전극 제조 공정을 국내 최초로 개발해, 상용 수준의 음이온교환막 수전해 스택에 적용하는 데 성공했다고 19일 밝혔다.
이 기술은 원스텝 열간 압착 공정으로, 원료물질인 코발트 수산화물을 촉매인 코발트 산화물로 변환하면서 동시에 고균일 촉매층을 형성하는 기술이다.
기존 공정(수산화물-산화물-분쇄-분산-코팅-건조)의 복잡한 공정 단계를 한 번의 코팅으로 대체했다.
이는 기존 공정 대비 60% 수준 간소화시킨 성과이며 동시에 균일한 촉매층 형성을 가능하게 했다.
또한 수소 발생 효율과 연속 운전 시 성능 감소율을 크게 개선했음을 확인했다.
연구팀은 원스텝 전극 제조 공정의 최적화를 위해 코발트(Co) 수산화물의 슬러리 조건과 열간 압착 공정의 핵심 인자인 온도 및 압력을 세밀하게 조절해, 10나노미터 크기의 균일한 산화물 입자로 구성된 촉매층 제조에 성공했다.
또한 개발된 전극을 음이온교환막과 수소발생촉매를 이용해 막전극접합체를 제조한 후, 상용 수준의 수전해 셀에서 이의 안정성과 성능을 확인했다.
연구팀은 개발된 전극을 음이온교환막 수전해 시스템에 적용함으로써, 높은 수소 발생 효율(저위발열량기준 수소 발생 효율 약 80퍼센트)과 낮은 성능감소율(연속 운전 1,000시간 동안 성능 감소율 2밀리볼트/킬로아워)의 안정적인 음이온교환막 수전해를 개발할 수 있음을 나타냈다.
수전해를 통한 그린수소 생산량은 2030년까지 1,100만톤, 69기가와트 용량을 가질 것으로 예상된다.
국내에서는 2024년 MW급 음이온교환막 수전해 시스템 실증을 위한 기술 개발을 추진하고 있으며, 2030년을 목표로 MW급 수전해 시스템 상용화를 추진하고 있다.
국내 음이온교환막 수전해 기술 수준은 선진국 대비 약 70∼80% 수준으로 관련 분야에 대한 많은 투자가 요구되며 핵심 원천 기술 확보와 기술 국산화가 시급하다.
본 기술 개발을 통해 양산 가능한 전극 제조 공정에 대한 원천기술을 확보함으로써 관련 기술의 글로벌 우위 확보와 수전해 기술 국산화 및 해외 수전해 시장 창출과 선점이 가능할 것으로 기대된다.
연구책임자인 재료연 최승목 책임연구원(UST 신소재공학과 부교수)은 “높은 공정 신뢰성을 가진 원스텝 열간 압착 전극 제조 공정을 개발해 음이온교환막 수전해의 상용화 관련 난제 중 하나를 해결했다”며 “본 기술이 적용되면 음이온교환막 수전해의 대량 양산이 가능해 단가를 크게 줄일 수 있을 것으로 기대한다”고 말했다.
본 연구성과는 한국연구재단의 중견연구자지원사업, 나노·소재기술개발(R&D) 국가전략기술소재개발 및 한국재료연구원의 기본사업의 지원을 받아 수행됐다.
또한 연구 결과는 어플라이드 에너지(Applied Energy) 誌에 6월5일 자로 게재승인 됐다(1저자: 명신우 박사과정(재료연, 울산과학기술원), 정재훈 기술기원(재료연)). 연구팀은 전류밀도 증가를 통한 수소생산량 증대, 수명 개선, 소재 및 부품 공정 양산화 기술 및 스택 운전 기술 개발 등 AEM 수전해 상용화를 위한 후속 연구를 진행하고 있다.