UNIST(울산과학기술원) 에너지화학공학과 정경민 교수팀은 리튬 이온 배터리의 건식 전극 단위 공정과 반제품 평가 방법을 새롭게 개발했다고 25일 밝혔다. 유해한 용매를 사용하지 않는 이 건식 공정은 배터리 성능을 높이면서 환경 보호에도 도움이 된다.
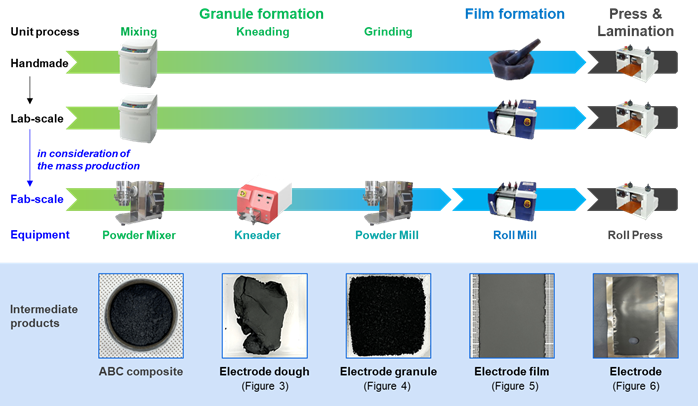
▲건식 전극 제조 공정
UNIST, 건식 전극 공정 상세 분석 상용화 가능성 제시
리튬 이온 배터리의 에너지 밀도를 높이면서도 유해 용매를 사용하지 않는 친환경 건식 전극 공정이 나왔다. 전기차와 다양한 전자기기의 에너지 사용이 한층 더 지속 가능해질 것으로 기대된다.
UNIST(울산과학기술원) 에너지화학공학과 정경민 교수팀은 리튬 이온 배터리의 건식 전극 단위 공정과 반제품 평가 방법을 새롭게 개발했다고 25일 밝혔다. 유해한 용매를 사용하지 않는 이 건식 공정은 배터리 성능을 높이면서 환경 보호에도 도움이 된다.
건식 공정의 세부 단계를 정의하고 각 단계가 배터리 성능에 미치는 영향을 세밀하게 분석함으로써 상용화에 한 걸음 더 다가섰다. 기존 연구가 성능 평가에 그쳤던 한계를 넘어선 것이다.
리튬 이온 전지 전극은 전통적으로 습식 공정으로 제작한다. 그러나 두꺼운 전극을 사용하면 바인더와 도전재의 불균일한 분포로 성능 저하 문제가 발생한다. 반면, 건식 전극 공정은 유기 용매를 사용하지 않아 균일한 전극을 만들 수 있지만, 상용화가 어려운 실험실 수준의 연구에 머물러 있다.
연구팀은 폴리테트라플루오로에틸렌(PTFE) 바인더 기반의 무용매 건식 공정을 도입해 제품화 가능성을 높였다. 공정은 과립 형성, 필름 형성, 압연 및 라미네이션 단계로 나뉜다. 각 단계에서 제작되는 반제품의 물리적, 전기적, 전기화학적 특성을 평가해 최적의 공정 조건을 찾았다.
특히 PTFE의 압출비가 높은 바인더를 사용하면 낮은 에너지로도 강도가 높은 전극 필름을 만들 수 있고, 전극의 미세 구조가 개선되어 출력 특성이 향상된다는 사실을 처음으로 밝혀냈다.
리튬 이온 배터리에서 바인더는 활물질과 전자를 이어주는 중요한 역할을 한다. 상용화된 습식 전극 공정에서는 바인더의 종류와 함량에 따라 공정과 전극의 성능이 크게 달라진다. 건식 전극에서도 PTFE 바인더의 종류와 함량에 따라 각 공정과 최종 전극의 출력 특성이 어떻게 바뀌는지 파악한 것이다.
정경민 교수는 “수작업으로 일일이 전극을 만드는 과정은 대량 생산이 어렵고, 일관된 품질을 유지하기 힘들다는 문제점이 있었다”며 “이번 연구는 실험실 규모를 넘어 단위 공정으로 세분화된 연구로 상용화에 기여할 것”이라고 강조했다.
제1저자 오혜성 연구원은 “이번 연구에서 PTFE의 종류와 함량에 따른 평가를 통해 전극의 출력 특성을 높일 실마리를 찾았다”며 “후속 연구를 통해 다양한 소재를 적용해 두꺼운 전극의 출력 특성을 더욱 향상하고 싶다”고 밝혔다.
이번 연구는 세계적인 화학공학 학술지인 Chemical Engineering Journal에 게재됐으며, 국가과학기술연구회(NST)가 지원하는 창의형 융합연구사업 ‘탄소중립형 고에너지밀도 배터리를 위한 소재/공정 혁신 융합 솔루션 개발’ 과제를 통해 수행됐다.
한편 공동 연구 중인 한국에너지기술연구원과 (주)한화는 건식 전극 특화 제조 장비를 제작 후 올해 하반기부터 실증할 예정이다.