한국재료연구원(KIMS, 원장 최철진) 나노재료연구본부 김태훈, 이정구 박사 연구팀이 연세대학교 이우영 교수 연구팀과 공동 연구를 통해 고가의 중희토류를 사용하지 않고도 고성능 영구자석을 제작할 수 있는 2단계 입계확산공정을 세계 최초로 개발하며, 희소자원 의존으로부터 해방될 것으로 기대가 모아진다.
.jpg)
▲중희토류 의존 없는 2단계 입계확산공정을 개발한 재료연 연구팀
재료연구원, 2단계 입계 확산공정 세계 최초 개발
고가의 중희토류가 없이도 하이엔드급 성능을 나타내는 영구자석 개발에 성공해, 희소자원 의존으로부터 해방될 것으로 기대가 모아진다.
한국재료연구원(KIMS, 원장 최철진)은 나노재료연구본부 김태훈, 이정구 박사 연구팀이 연세대학교 이우영 교수 연구팀과 공동 연구를 통해 고가의 중희토류를 사용하지 않고도 고성능 영구자석을 제작할 수 있는 2단계 입계확산공정을 세계 최초로 개발했다고 3일 발표했다.
이번 연구로 개발된 영구자석은 전기차 모터와 로봇 등 다양한 고부가가치 제품에 핵심 부품으로 사용될 수 있다.
기존 영구자석 제조 공정은 중국이 독점적으로 생산하는 중희토류에 의존하여 자원 의존도가 높고 원가가 비싸다는 한계가 있었다.
반면에 이번 연구를 통해 고가의 중희토류 없이도 하이엔드급의 강력한 성능을 구현하는 영구자석 개발에 성공했다.
2단계 입계확산공정은 자석의 성능을 향상시키기 위한 기술로, 자석 표면에 필요한 물질을 얇게 도포하고 고온에서 열처리하여 물질이 자석 내부에 들어가면서 보자력 등 성능을 향상시킨다.
연구팀이 개발한 공정은 1단계에서 고융점 금속이 포함된 신물질을 영구자석 표면에 고온 침투시키고 상온에서 냉각 처리한 후, 2단계에서 저가의 경희토류(Pr, 프라세오디뮴) 함유 물질을 재도포해 고온 처리하는 방식이다.
이를 통해 확산물질이 자석 내부에 빠르게 침투하여 경희토류를 사용했음에도 중희토류를 사용한 상용자석과 동등한 등급의 성능을 구현할 수 있었다.
이번 기술이 상용화되면 고효율 모터를 요구하는 전기자동차, 드론, 플라잉카와 같은 고부가가치 산업 분야에서 영구자석의 제조 원가 절감과 성능 향상을 모두 충족할 것으로 기대된다.
연구책임자인 김태훈 선임연구원은 “현재 전기자동차와 고급 가전의 모터에 사용되는 자석에는 고가의 중희토류 사용이 불가피하지만, 이번 기술은 새로운 개념을 도입해 고급 자석 제조에서 중희토류 의존을 탈피할 가능성을 보여줬다”며 “이번 연구가 영구자석 분야의 핵심 공정인 입계확산공정 관련 연구의 새로운 방향을 제시했다”고 설명했다.
이번 연구는 과학기술정보통신부와 한국연구재단-나노 및 소재기술개발사업의 지원을 받아 진행됐으며, 연구결과는 세계적인 학술지 ‘액타 머터리얼리아(Acta Materialia)’에 12월24일자로 온라인 게재됐다.
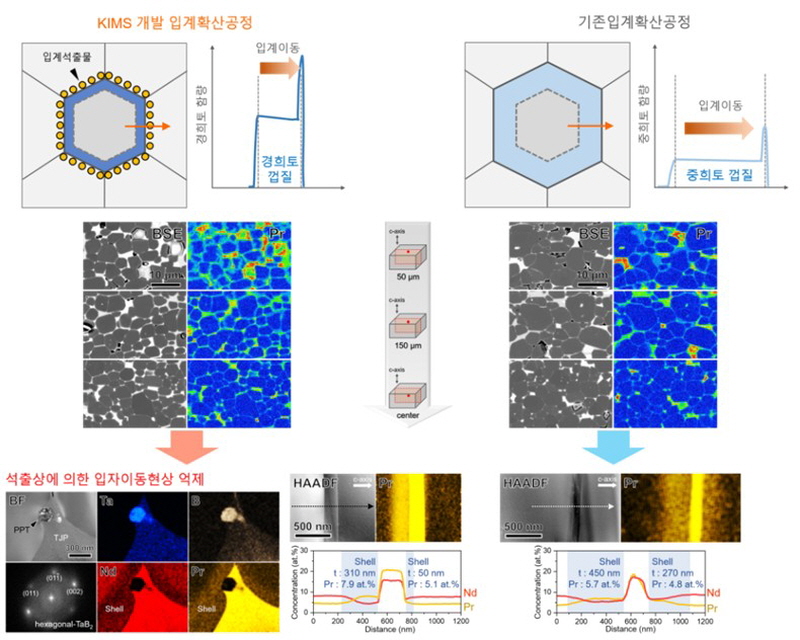
▲입계확산공정 기술 개발 모식도 및 실제 분석 데이터